Are you looking for a way to measure the liquid level in a hazardous area without any risk of explosion? Then an explosion proof ultrasonic level sensor might be exactly what you need. This instrument can accurately measure the distance between the sensor and the liquid level without any contact, using ultrasonic waves. It is an intrinsically safe solution that is suitable for use in a variety of environments, from fuel tanks to water reservoirs.
In this article, we will guide you through the process of choosing the right explosion proof ultrasonic level sensor for your needs. We will discuss the key factors to consider,, and give you tips on how to make an informed decision.
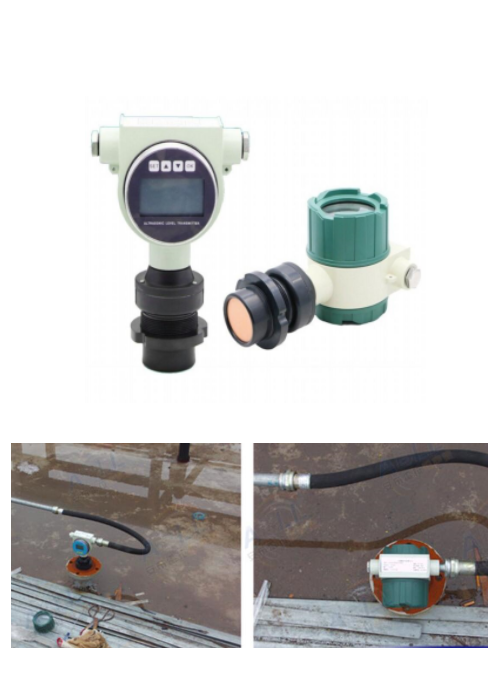
Explosion Proof Ultrasonic Level Sensors Operating Principle
Explosion-proof ultrasonic level sensors are devices designed to measure the level of liquids or solids in hazardous environments, where explosive gases or dusts are present. They are specifically constructed to prevent explosions by using materials and designs that can withstand sparks or high temperatures.
Explosion-proof ultrasonic level sensors use sound waves to measure liquid levels without touching the liquid. The sensor emits high-frequency sound waves that bounce off the surface of the liquid and calculate the distance between the sensor and the liquid level. This reading can be displayed on a screen or transmitted to a control system. These sensors are safe for hazardous environments because they don’t touch the liquid.
Read more about: Ultrasonic level measurement
Factors to Consider When Choosing Explosion Proof Ultrasonic Level Sensors
Explosion Proof Ultrasonic Level Sensor is a non-contact liquid level measuring instrument that is easy to install and maintain. It is widely used to measure flammable and explosive liquids such as diesel oil and crude oil, or to measure the height of liquids in explosion-proof environments.
When selecting an explosion-proof ultrasonic liquid level sensor, the following points need to be considered:
- The type of medium to be measured (liquid or solid, specific name: clean water, sewage, mud, gasoline, diesel, toluene, sulfur dioxide, etc.).
- If liquid: Is there steam, fog, foam, waves, agitation, floating objects on the level?
- If solid: is it solid? Is there dust?
- Minimum to maximum temperature and minimum to maximum pressure of the medium;
- Corrosive to the medium. If it is placed in a tank, it is necessary to know the material of the tank and whether there is an anti-corrosion lining;
- Whether explosion-proof and anti-corrosion are required;
- Working environment: such as open ponds, covered ponds, horizontal tanks, vertical tanks, spherical tanks, storage tanks, etc.;
- Working voltage: 24VDC or 220VAC;
- Output signal: 4~20mA current, 485 communication output, relay output;
- Equipment type: split or integrated.
Featured Explosion Proof Ultrasonic Level Sensors we supply.
Explosion Proof Ultrasonic Level Sensor Price
Of course, in addition to the above parameters, the price is also one of the important parameters we need to consider. Sino-Inst manufactures and supplies Explosion Proof Ultrasonic Level Sensors. Has a price advantage. Refer to Explosion Proof Ultrasonic Level Sensor FOB price USD 470.00/pc.
You can contact our sales engineers to get detailed prices, or apply for sales discounts!
Read more about: What Is the Difference Between Class 1 Div 1 and Class 1 Div 2 ?
Notes on Explosion Proof Ultrasonic Level Sensor
- If the instrument is used outdoors, a sun visor or a protective box should be installed. To prevent the LCD screen from aging due to long-term sunlight exposure.
- If it is used in an environment with corrosive gas, an anti-corrosion sleeve must be installed, and the instrument shell and the inlet and outlet terminals must be tightened.
- If it is used in a place with corrosive gas or liquid, or at the seaside or at sea, the anti-corrosion type must be selected.
- The wire and cable protection tube should be sealed to prevent water accumulation and bites by rodents such as mice.
- Although the instrument has its own lightning protection device. However, when using the instrument in an area prone to lightning strikes, it is recommended to install a special lightning protection device at the entrance and exit of the instrument.
- When the instrument is used in a particularly hot and cold place, that is, when the ambient temperature may exceed the working requirements of the instrument, it is recommended to install a high and low temperature protection device around the liquid level instrument.
- The ultrasonic probe should be perpendicular to the measured liquid level, and there should be no other obstacles within the range of the ultrasonic emission cone.
- For use at <20°C or >60°C, please contact the technical service department in advance.
- There is dust, steam and mist in the environment. If there are foams, floats, liquid agitation, waves, etc., please contact the technical service department first.
Read more about Advantages Of Ultrasonic Level Sensors.
More Ultrasonic Level Sensor Applications and Markets
Ultrasonic Level Sensor for Diesel Tanks | 5~150cm,0-30m
Non Contact Level Transmitters: Types & Industrial Applications
Tech Guide for Non-Contact Radar Type Level Transmitters
Contact and Non-contact | Capacitive water level sensor
Ultrasonic Water Level Sensors
Procurement Guide: Ultrasonic liquid level sensors
More Explosion Proof Level Sensors
An explosion proof level sensor is a type of sensor that is housed within a durable casing capable of containing an explosion or flame. This type of sensor is utilized in situations where it is not feasible to decrease the amount of electrical circuit energy being used.
Sino-Inst provides a variety of Explosion Proof Level Sensors, which have passed the CNEX explosion-proof certification.
Read more about: Ultrasonic Level Sensors for Liquids Applications
In conclusion, choosing the right explosion proof ultrasonic level sensor is crucial for ensuring safety and accuracy in hazardous environments.
When selecting a sensor, it is important to consider factors such as the application environment, accuracy requirements, and certifications compliance. By understanding these key factors and evaluating the top products available on the market, you can make an informed decision that meets your specific needs.
Remember to always prioritize safety and follow installation and maintenance procedures carefully. With the right explosion proof ultrasonic level sensor, you can accurately measure liquid levels without any risk of explosion.
Request a Quote
Wu Peng, born in 1980, is a highly respected and accomplished male engineer with extensive experience in the field of automation. With over 20 years of industry experience, Wu has made significant contributions to both academia and engineering projects.
Throughout his career, Wu Peng has participated in numerous national and international engineering projects. Some of his most notable projects include the development of an intelligent control system for oil refineries, the design of a cutting-edge distributed control system for petrochemical plants, and the optimization of control algorithms for natural gas pipelines.