Submersible water level sensors are important tools used to measure water levels in various applications. These pressure level sensors can be found in wells, water tanks. They work by using a probe for hydrostatic level measurement, which measures the pressure created by the water depth.
A submersible pressure sensor, also known as a pressure transducer, can be used in deep wells and tanks to control the pump and manage water flow. Some sensors also connect to LoRaWAN networks for remote monitoring. Submersible water level sensors provide accurate data to ensure proper water levels in any application.
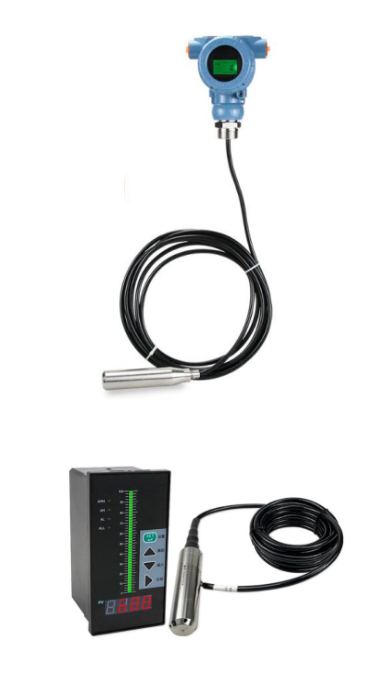
Featured submersible water level sensorrs from Sino-Inst
Advantages of submersible water level sensors for Tanks & Groundwater
Submersible water level sensors offer several advantages for tanks and groundwater applications:
- Accuracy: These sensors provide precise measurements of water levels, ensuring proper management of resources. The conventional accuracy is 0.5%. High precision 0.2% can be customized;
- Durability: Built to withstand harsh conditions, they last a long time. Stainless steel, or PTFE and other materials are optional.
- Ease of installation: They can be easily installed in various environments, including deep wells and tanks, without the need for complicated equipment.
- Real-time monitoring: Connected to monitoring systems, they deliver up-to-date information on water levels, allowing for informed decision-making.
- Cost-effective: Submersible sensors often require less maintenance and have lower long-term costs compared to other water level monitoring methods.
- Versatility: They can be used in a wide range of applications, from residential water tanks to industrial groundwater management systems.
submersible water level sensor for Harsh Applications
Submersible water level sensors can work well in extreme temperatures, high pressure, and even in the presence of corrosive chemicals.
Whether you need to monitor water levels in a wastewater treatment plant or a chemical storage tank, a submersible water level sensor is an ideal choice for your harsh application needs.
On the one hand, we can choose anti-corrosion materials to measure corrosive liquids. Such as PTFE material.
On the other hand, we can choose anti-blocking probe. For example, when measuring wastewater and sewage.
Read More About:
- Wastewater Level Sensor for Septic Tank-Sewage Holding Tank
- Water Level Monitoring Sensor/System for Sewage-Wastewater
submersible water level sensor for deep well
A submersible water level sensor is perfect for deep wells because it can accurately measure water levels even in great depths. Regular ranges are 100m, 200m, 300m. Special designs can be customized up to 2000m.
These sensors are designed to work under high pressure and can handle the challenges of being submerged for long periods.
By installing a submersible sensor in a deep well, you can get real-time data on the water level, which helps manage the water supply effectively. This ensures that the well pump works efficiently and prevents over-pumping or dry-running.
Read more about: Upgraded Water Well Depth Measuring Devices
More about Submersible pressure sensors
More Featured Water Level Sensors
Level Measurement Solutions
Reliable Industrial Tank Level Monitoring System
Top 5 Ultrasonic Level Sensor Applications
Ultrasonic Depth Sensor vs Ultrasonic Level Sensor
How to Measure River Water Level?
New Choice for Heating Oil Tank Level Sensor
How to Choose the Right Diesel Fuel Level Sensor ?
In conclusion, submersible water level sensors play a crucial role in monitoring liquid levels in various applications such as tanks, wells, and sewage systems. By understanding how these sensors work, their construction, and the concept of hydrostatic pressure, you can make informed decisions when selecting the right sensor for your needs.
As you consider your options, remember that we, at Sino-Inst, are a professional manufacturer of submersible water level sensors. With years of experience, we are committed to providing high-quality, reliable sensors for all your level monitoring requirements. Our expertise ensures that you get the best sensor for your application, so you can enjoy accurate measurements and peace of mind.
Don’t hesitate to reach out to us for more information or to discuss your specific needs. We are here to help and guide you through the process of selecting the perfect submersible water level sensor for your project. Choose Sino-Inst, and experience the difference that a professional manufacturer can make. Contact us today!
Request a Quote
Wu Peng, born in 1980, is a highly respected and accomplished male engineer with extensive experience in the field of automation. With over 20 years of industry experience, Wu has made significant contributions to both academia and engineering projects.
Throughout his career, Wu Peng has participated in numerous national and international engineering projects. Some of his most notable projects include the development of an intelligent control system for oil refineries, the design of a cutting-edge distributed control system for petrochemical plants, and the optimization of control algorithms for natural gas pipelines.