What is a pressure sensor?
A pressure sensor is a device that senses a pressure signal and converts the pressure signal into a usable output electrical signal according to certain rules.
Pressure sensors have a variety of structural types. Common types are strain gauge, piezoresistive, capacitive, piezoelectric, vibration frequency pressure sensors.
Pressure sensors are mainly used in booster cylinders. Pneumatic-hydraulic booster cylinder. Gas-hydraulic booster. Air conditioning and refrigeration equipment and other fields.
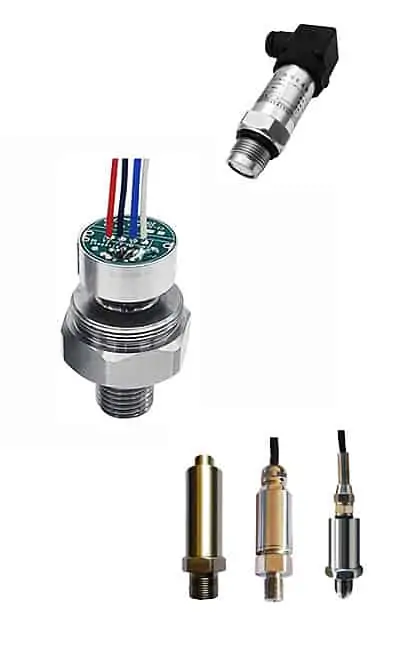
Types of pressure sensors
Pressure sensors can be classified according to the pressure range they measure, their operating temperature range or the type of pressure they measure. In terms of pressure type, pressure sensors can be divided into several major categories.
Absolute pressure sensors
Absolute pressure sensors measure pressure relative to an ideal vacuum pressure (0 PS or no pressure). With reference to vacuum, the atmospheric pressure at sea level is 101.325 kPa (14.7PSI).
Gauge Pressure Sensors
Gauge pressure sensors are used in different applications because they can be calibrated to measure pressure relative to a given atmospheric pressure at a given location. A tire pressure gauge is an example of a gauge pressure indication. More about: What is Diaphragm pressure gauge?
Vacuum Pressure Sensors
Vacuum pressure sensors are used to measure pressures that are less than atmospheric pressure at a given location.
Differential Pressure Sensor
A differential pressure sensor or transmitter measures the difference between two or more pressures introduced as inputs to a sensing unit. An example is the measurement of the pressure drop across an oil filter. Differential pressure is also used to measure the flow or level in a pressurized vessel.
Sealed Pressure Sensors
Extended reading: Featured Diaphragm Seal Pressure Transmitters
A sealed pressure transducer is similar to a gauge pressure transducer, except that it has been calibrated by the manufacturer to measure pressure relative to sea level pressure.
More about Industrial Pressure Sensors
Featured Pressure Sensors
Working Principles of Pressure Sensors
Pressure Sensors are devices that convert various pressures into another physical quantity (usually electricity) that can be easily processed and transmitted according to certain rules. pressure sensors generally consist of three parts: a sensitive element, a conversion element and a measurement circuit, sometimes with an additional auxiliary power supply.
Extended Reading: Digital Pressure Sensor-RS485
Let’s look at the technology used in pressure sensors in more detail.
Pressure measurement technologies
Extended reading: Pressure indicator transmitters
Pressure sensors, pressure transducers, and pressure transmitters
A pressure sensor is a device or device that can sense a pressure signal and convert the pressure signal into a usable output electrical signal according to a certain rule.
A pressure sensor usually consists of a pressure-sensitive element and a signal processing unit. According to different test pressure types, pressure sensors can be divided into gauge pressure sensors, differential pressure sensors and absolute pressure sensors. A pressure sensor is the core part of pressure transmitter.
In a pressure transducer, a thin-film or piezo-resistive pressure sensor is mounted on a process connection. The transducer converts pressure into an analog electronic output signal, typically as a millivolt per volt output. These signals are not linearized or temperature compensated.
A pressure transmitter has additional circuitry that linearizes, compensates, and amplifies the signal from a transducer. The different signal types are typically voltage signals (eg, 0 to 5 or 0 to 10 volts), milliamp (eg, 4 to 20 milliamp), or digital. The instrument can transmit the signal to a remote receiver.
Extended reading: Static pressure vs dynamic pressure vs total pressure
Pressure sensor performance parameters
Pressure sensors mainly have the following parameters.
1.Capacity.
The range refers to the rated load of the pressure sensor. The general unit is KGf, N, etc.. Such as the range of 100KGf, the sensor measurement range is 0-100KGf.
2. Rated output.
Sensitivity is the output signal coefficient of the pressure sensor, the unit is mV / V, common 1mV / V, 2mV / V, the full range of the pressure sensor output = working voltage * sensitivity, for example: working voltage 5VDC, sensitivity 2mV / V, the full range of output that is 5V * 2mV / V = 10mV, such as pressure sensors full range of 100KG, pressure full 100KG, the output that is 10mV, pressure 50KG that is 5mV.
3. Non-linearity.
Non-linearity is the percentage of the maximum deviation between the output value of the empty load and the output value of the rated load determined by the straight line and the actual measured curve of the increased load for the rated output value. In theory, the output of the sensor should be linear, but in fact it is not. Non-linearity is the percentage deviation from the ideal. Non-linear units: %FS, non-linear error = range * non-linearity, such as the range of 100KG, non-linearity of 0.05% FS, non-linear error that is: 100KG * 0.05% = 0.05KG.
4. Repeat ability.
Repeatability error refers to the repeated loading of the sensor to the rated load and unloading under the same environmental conditions. The maximum difference of the output value on the same load point during the loading process on the percentage of rated output.
5.Creep.
Creep refers to the load remains unchanged, other test conditions also remain unchanged, the pressure sensor output change over time on the percentage of rated output, generally taken 30min.
6.Hysteresis.
Hysteresis refers to the pressure sensor from no load gradually loaded to the rated load and then gradually unloaded. In the same load point on the maximum difference between the loaded and unloaded output on the rated output value of the percentage.
7. Zero balance.
Under the recommended voltage excitation, the output value of the pressure sensor at no load is a percentage of the rated output. Theoretically, the output of the pressure sensor at no load should be zero, in fact, the output of the pressure sensor at no load is not zero, which there is a deviation, zero output is the percentage of deviation.
8.Input resistance.
Input resistance is the signal output open circuit, the sensor is not pressurized, from the pressure sensor input (Cang positive pressure sensor for the red and black line) measured impedance value.
9.Output resistance.
Output resistance is a short circuit at the input of the pressure sensor, the sensor is not pressurized, the impedance measured from the signal output (Cangzhou pressure sensor for the green and white lines).
10.Insulation impedance.
Insulation impedance is the DC impedance value between the circuit of the pressure sensor and the elastomer.
11.Operation Temp range.
Operating temperature range refers to the pressure sensor in the temperature range of its performance parameters will not produce permanent harmful changes.
12. Compensated temp range.
Temperature compensation range refers to the temperature range, the rated output of the sensor and zero balance are closely compensated, so as not to exceed the specified range.
13. Temperature effect on zero.
Temperature effect on zero refers to the effect of changes in ambient temperature on the zero point of the pressure sensor. Generally used for every 10 ℃ change in temperature, the amount of change in zero balance caused by the percentage of the rated output to express, the unit: % F.S./10 ℃.
14. Temperature effect on out.
Sensitivity temperature drift is the change in the sensitivity of the pressure sensor caused by changes in ambient temperature. Generally expressed as a percentage of the rated output for each 10 ℃ change in temperature caused by the change in sensitivity, the unit is: F.S./10 ℃.
15. Safe Load Limit.
Safe overload means that the load will not cause destructive damage to the pressure sensor, but can not be overloaded for a long time.
16. Ultimate overload.
Ultimate overload is the limit value of the pressure sensor load.
17. Excitation voltage Excitation recommend.
Excitation voltage refers to the working voltage of the pressure sensor, generally 5-12VDC.
Extended Reading: Up to 800°C High Temperature Pressure Sensor
Applications of Pressure Sensors
Pressure sensor is one of the most commonly used sensors in industrial practice. It is widely used in various industrial self-control environments. It involves water conservancy and hydropower, railroad transportation, intelligent building, production automation, aerospace, military, petrochemical, oil well, electric power, ship, machine tool, pipeline and many other industries.
The following is a brief introduction to some application examples of pressure sensors.
- Application to hydraulic system
Pressure sensor in the hydraulic system is mainly to complete the closed-loop control of the force. When the control valve spool moves suddenly, a spike pressure of several times the working pressure of the system will be formed in a very short period of time.
- Pressure sensors in the application of water treatment
China’s environmental protection water treatment industry, in recent years, has been rapid development, and the future prospects are promising. Water and wastewater treatment processes rely on the use of pressure sensors to provide an important means of control and monitoring for system protection and quality assurance.
- Application in injection molding
Pressure sensors have an important role in injection molds. Pressure sensors can be installed in the nozzles of injection molding machines, hot runner systems, cold runner systems and mold cavities to measure the plastic pressure somewhere between the nozzle of the injection molding machine and the mold cavity during the injection, filling, holding and cooling processes.
- Applications in compressors, air conditioning and cooling equipment
Pressure sensors are commonly used in air compressors and air conditioning and refrigeration equipment. These sensors are compact and easy to install, and the pressure guide port is usually designed with a special valve needle.
- Used in monitoring mine pressure
Sensor technology as one of the key technologies for mine pressure monitoring.
On the one hand, we should properly apply the existing variety of sensors to serve the mining industry;
On the other hand, sensor manufacturers develop and develop new pressure sensors to adapt to more mining industry applications.
Note that the pressure transmitter needs to be calibrated after a period of use. In order to ensure the accuracy of the quantity.
FAQ
Related Blogs
What is a pressure sensor? and other questions about pressure sensors. We hope that after reading this article, you will have a clear understanding.
Sino-Inst offers over 20 Pressure sensors. A wide variety of Pressure sensors options are available to you. Such as free samples, paid samples.
Sino-Inst is a globally recognized manufacturer of Pressure sensors, located in China. Sino-Inst sells through a mature distribution network that reaches all 30 countries worldwide. Pressure sensors products are most popular in Europe, Southeast Asia, and Mid East. You can ensure product safety by selecting from certified suppliers. With ISO9001, ISO14001 certification.
Wu Peng, born in 1980, is a highly respected and accomplished male engineer with extensive experience in the field of automation. With over 20 years of industry experience, Wu has made significant contributions to both academia and engineering projects.
Throughout his career, Wu Peng has participated in numerous national and international engineering projects. Some of his most notable projects include the development of an intelligent control system for oil refineries, the design of a cutting-edge distributed control system for petrochemical plants, and the optimization of control algorithms for natural gas pipelines.