Dew Point Meter for Compressed Air Systems are crucial for efficient, safe industrial operations. These devices keep moisture levels in check, safeguarding your equipment and boosting productivity. Here, we’ll explore the ‘whys’ and ‘hows’ of dew point meters and introduce our state-of-the-art product – designed with industry needs in mind.
Sino-Inst offers a range of dew point meters for compressed air and gas systems.
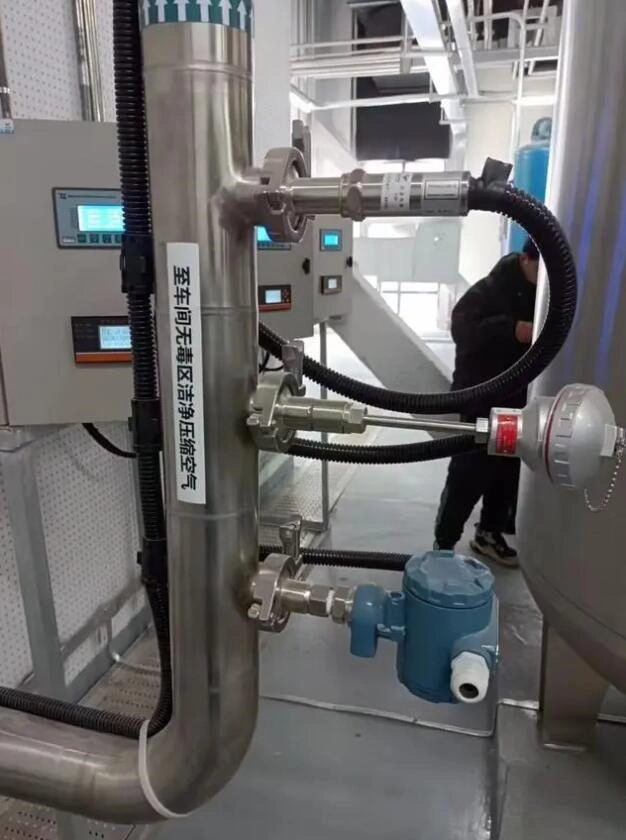
Compressed air systems are key in industries for cooling, heating, and running tools. During this process, water vapor can form. It’s okay in small amounts, but too much can harm equipment and reduce product quality. So, monitoring the dew point, or the temperature where water vapor turns into liquid, becomes really important.
Featured Dew Point Meter for Compressed Air
What is the dew point of a compressed air system?
Air compressor system dew point is the temperature at which water vapor condenses to a liquid state at the same rate as evaporation. At this temperature, compressed air is completely saturated and can no longer hold water vapor. For industrial operators using compressed air systems for manufacturing, continuous monitoring of dew point is essential to prevent instrument damage and minimize process contamination.
Is dew point measured in degrees?
Use a dew point transmitter to measure the dew point temperature of compressed air in degrees Fahrenheit. For most systems, the dew point temperature of the air is maintained in the range of 50°F to 94°F. At this temperature, water suspended in the air can settle and begin to collect on compressor components.
If read accurately, a dew point sensor will allow operators to implement different methods of water removal and maintain the integrity of their machinery.
Why is dew point important in compressed air applications?
Maintaining moisture levels is critical to maintaining the functionality of sensitive industrial equipment. If left unchecked, moisture precipitated from compressed air at its dew point can cause mechanical corrosion of metals. This can lead to costly system failures and downtime for maintenance.
Additionally, excess moisture in the compressed air supplied to industrial processes can adversely affect product quality. Accumulated water vapor can transfer impurities such as dust and bacteria into sensitive food and pharmaceutical manufacturing processes. As a result, its output is unsafe and cannot be safely eaten.
The bad effects of moisture damage to an air compressor system is why all operators must rigorously monitor the water saturation in their air systems.
The harm caused by water in compressed air is mainly manifested in:
- It will take away the lubricating oil on the pneumatic equipment, resulting in reduced efficiency or even damage to the equipment;
- It will cause the wear of the valve in the pipeline, resulting in the failure or misoperation of the pneumatic control equipment;
- Corrosion of pipelines and equipment;
- If water freezes at the low point of the pipeline, the pipeline is still in danger of bursting;
- If the compressed air used for spraying contains water mist, it will affect the adhesion of the paint on the workpiece, resulting in failure of the paint;
- It will cause risks such as internal corrosion or blockage of industrial equipment and machinery, reduce the smoothness of the inner surface of the pipeline, and cause pressure loss;
Therefore, to avoid condensation due to high moisture content in the compressed air, the compressed air must be dried to a dew point below the temperature of the coldest surface anywhere in the gas piping system.
Dew point and pressure relationship
There is a clear link between the dew point at which compressed air reaches saturation and the pressure at which it is delivered. As with any gas, an increase in pressure results in a corresponding increase in its dew point. A series of calculations and conversions are done manually or using software that can accurately predict the air dew point and help the operator develop an appropriate dehumidification protocol. The handheld temperature and humidity meter can automatically convert the detected temperature and humidity data into a dew point value, which is convenient for real-time viewing.
How is dew point different from pressure dew point?
In practice, the terms “dew point” and “pressure dew point” are often used interchangeably. However, this substitution is not accurate.
The dew point is the temperature at which air becomes saturated at atmospheric pressure.
Whereas pressure dew point is defined as the dew point of a gas measured at a pressure above normal atmospheric pressure.
Dew Point Meter for Compressed air range selection
For most air compressors, the type of dryer used determines the dew point range of its dew point meter. Common compressed air dryers include adsorption and freeze drying.
Freeze drying is a technology that uses the principle of sublimation to dry. The water dew point of the freeze dryer is generally around -20°C.
Adsorption drying is dehydration and drying by using the adsorbent’s selective adsorption of water vapor in compressed air. The dew point of the adsorption dryer is -60°C to -70°C or below.
Therefore, the range of the freeze-drying dew point meter is usually -60°C-60°C, and the range of the adsorption type dew point meter is -80°C-20°C, or -100°C-20°C.
FAQ
More compressed air Measurement Solutions
More than Just Compressed Air! What Gases Can the Dew Point Meter Detect?
Top 1 Guide to Dew Point Measurement
What Is a Doppler Flow Meter?
Compressed Air Flow Meter
Industrial Gas Pressure Sensors and Transducers – Gas Pressure Measurement
Digital Gas Flow Meters & Controllers List For Air-O2-N2-CO2
In conclusion, understanding and managing the dew point in your compressed air system is crucial to ensuring the longevity of your machinery and maintaining high-quality production. Our “Dew Point Meter for Compressed Air” offers a precise, easy-to-use solution for monitoring this essential parameter in your operation.
Don’t leave the health of your machinery and the quality of your products to chance. Equip your operations with our advanced Dew Point Meter for Compressed Air today.
Request a Quote
Wu Peng, born in 1980, is a highly respected and accomplished male engineer with extensive experience in the field of automation. With over 20 years of industry experience, Wu has made significant contributions to both academia and engineering projects.
Throughout his career, Wu Peng has participated in numerous national and international engineering projects. Some of his most notable projects include the development of an intelligent control system for oil refineries, the design of a cutting-edge distributed control system for petrochemical plants, and the optimization of control algorithms for natural gas pipelines.