Stainless steel flow meter with stainless steel housing and stainless steel flange connection. Stainless steel flow meter can be used in harsh environment for corrosive fluids flow measurement.
Stainless steel flow meter is an electromagnetic flow meter made of stainless steel. It works based on Faraday’s law of electromagnetic induction. Used to measure the volume flow of conductive liquids with conductivity greater than 5μS/cm. Stainless steel flow meter is an induction meter that measures the volume flow of conductive media. It can measure the volume flow of general conductive liquids. It can also be used to measure the volume flow of strong corrosive liquids such as strong acids and alkalis and even liquid-solid two-phase suspension liquids such as mud, mineral pulp, and paper pulp.
Sino-Inst offers a variety of Magnetic Flow Meters for flow measurement. If you have any questions, please contact our sales engineers.
Features of Magnetic Stainless Steel Flow Meter
- Flow measurement is not affected by changes in flow density, viscosity, temperature, pressure and conductivity. The sensor induced voltage signal has a linear relationship with the average flow rate. Therefore, the measurement accuracy is high
- There is no obstruction in the measuring pipe, so there is no additional pressure loss. There are no movable parts in the measuring pipeline. So the sensor has a long life
- The straight pipe section required by the sensor is short, which is convenient for installation
- Only the inner lining and electrode of the sensor are in contact with the liquid to be measured. As long as the electrode and lining material are selected reasonably. Resistant to corrosion and wear
- Two-way measurement system. The forward and reverse flow can be measured.
- Applicable medium: any conductive liquid.
Specifications of Magnetic Stainless Steel Flow Meter
Converter form | Compact type | Split type |
Executive standard | JB/T9248-1999 | JB/T9248-1999 |
Accuracy class | Level 1 or 0.5 | Level 1 or 0.5 |
Dielectric conductivity | >5μs/cm | >5μs/cm |
Can measure the lowest flow rate | 0.1 m/s | 0.1 m/s |
Can measure the highest flow rate | 15m/s | 15m/s |
Turndown ratio | 1:20, can be customized | 1:20, can be customized |
monitor | Standard | Standard |
Signal output | Pulse or 4-20mA | Pulse or 4-20mA |
Lining material | Rubber, PTFE | Rubber, PTFE |
Electrode material lining | 316 stainless steel, tantalum, titanium | 316 stainless steel, tantalum, titanium |
Power supply | 220VAC or +24VDC | 220VAC or +24VDC |
Communication Interface | RS232, RS485 | RS232, RS485 |
Protocol | MODBUS, HART, Profibus, etc. | MODBUS, HART, Profibus, etc. |
Explosion-proof grade | Exd[ia]qIICT5 | Exd[ia]qIICT5 |
Protection level | IP65, optional IP68 | IP65, optional IP68 |
Instrument pass | DN6~DN2000 | DN6~DN2000 |
Installation method | Flange installation, optional flange clamping | Flange installation, optional flange clamping |
Nominal pressure | 1.6MPa or customized | 1.6MPa or customized |
Medium temperature | <180℃ | <180℃ |
Ambient temperature | -30℃-60℃ | -30℃-60℃ |
Flow Meter for Measuring Corrosive Liquids
Stainless Steel Flow Meter is a kind of electromagnetic flow meter. It can be used to measure the flow of strong corrosive liquids such as acid, alkali and salt solution.
In the process of industrial consumption, many media are slightly or extremely corrosive. However, due to consumer demand, we also need to measure these media.
How to choose a suitable flow meter? How to choose a flow meter for measuring corrosive media?
1.Corrosion
Corrosion is a phenomenon in which metals are destroyed due to chemical effects in their environment. All metals and alloys can be corrosion resistant in certain specific environments.
But in other environments it is very sensitive to corrosion. Generally speaking, there are no industrial metal materials that are resistant to corrosion in all environments.
Corrosion can be divided into uniform corrosion (uniform corrosion) or general corrosion (general corrosion) and partial corrosion (localized corrosion).
The corrosion rate of general corrosion can be expressed in units such as mm/a. Usually, the data whose corrosion rate is below 0.1mm/a is converted to corrosion-resistant data. The corrosion rate is one order of magnitude larger than this, that is, the corrosion rate is 1mm/a.
Information about common equipment can sometimes be determined as applicable. Regarding the measuring element of the flow meter, it is not allowed. Based on the corrosion rate, the service life of the metal can be predicted.
Extended reading: Corrosive Liquid Chemical Level Sensor in Chemical Processing
2.Damage to the flowmeter caused by corrosive media
The corrosiveness of the medium is a serious threat to the flowmeter. Only certain types of flow meters such as clamp-on ultrasonic flow meters are less affected by corrosion.
a. Corrosive media will corrode the parts that are in direct contact with the flowmeter. Make it damaged and lose its function. For example, corrosion damage to the diaphragm of the differential pressure transmitter, and complete failure due to leakage of silicone oil. The electrode is corroded, causing the medium to be out of the world, causing the excitation coil to burn out.
b. The parts of the flowmeter are corroded by corrosive media for a long time and the geometric dimensions are changed. Cause the accuracy of the instrument to decrease. For example, after the rotor in the rotameter is corroded by the fluid, the outer dimension is reduced.
As a result, the flow indication is low. Another example is that the vortex generator in the vortex flowmeter is corroded by the fluid and the width is reduced. The appearance of the front flow surface becomes rough, causing changes in the flow coefficient.
There are also clamp-on ultrasonic flowmeters that are less affected by corrosive media. It is also often caused by the corrosion of he metal pipe by the medium. It weakens the transmitting and receiving signals, and loses flexibility in severe cases.
c. Shorten the life of the instrument. For example, the conical tube and other parts in the metal tube float flowmeter. After several years, the welds were worn out.
d. Leakage of corrosive media. If it is not discovered and disposed of in time, it will easily lead to safety and personal accidents.
According to long-term inspection, electromagnetic flowmeter and ultrasonic flowmeter are selected for common corrosive liquid measurement. If it is corrosive gas, you can choose acid-resistant stainless steel vortex flowmeter or other gas flowmeter.
The electromagnetic flowmeter for measuring liquid media can measure various corrosive media containing tiny particles. Of course, the premise is that the measured medium is conductive. It is only necessary to use different lining materials and electrode materials according to the corrosiveness of the medium to deal with the corrosion problem of the medium belt.
Ultrasound is even simpler. If you choose a clamp-on ultrasonic flowmeter, you don’t have to think about the corrosiveness of the medium at all. It’s just not as high as an electromagnetic flowmeter in measurement accuracy.
More Featured Stainless Steel Flow Meters
3.Measures for fluid corrosion in flow measurement
(1) Change the instrument regularly
Corrosive media can corrode metals in various conditions. Some corrosion rate is very fast, that is, full corrosion. Some corrosion is subtle, very slow, that is, partial corrosion. When making instrument selection, it should be analyzed in detail according to the detailed situation. Then make a decision.
For example, compressed air and water are generally considered to be non-corrosive, but they are not. Because the concentration of nitrogen and oxygen compounds in the atmosphere in urban areas is generally higher. When it is absorbed by the condensate in the compressed air. The condensate is acidic. Thereby it has slight corrosion to carbon steel materials.
This situation is more serious in plant areas such as sulfuric acid plants, nitric acid plants, and chlor-alkali plants. Of course, in addition to dilute nitric acid, sulfuric acid and hydrochloric acid may be contained in the compressed air at this time. The water situation is similar. Especially river water. Because it contains a variety of ions, it also corrodes carbon steel. Instruments used under this condition will show signs of corrosion after several years.
For example, it was found that the surface of the carbon steel ring chamber in contact with the fluid in the flow throttling installation was corroded. Become bumpy. In severe cases, the geometric size and appearance will change greatly. The inner walls of the front and rear straight pipe sections also become uneven. This situation does not meet the requirements of the verification procedures. It is difficult to guarantee the accuracy of the original instrument.
At this time, a problem arises. Is it possible to design and select the annular chamber and the front and rear straight pipe sections in the throttling installation to be changed to stainless steel?
Of course, if it is changed to stainless steel. The corrosion problem of the annular chamber and straight pipe section will certainly be solved, but at the same time the investment has increased. And the increase in investment is related to the pipe diameter. If the nominal diameter is larger. The increase in technology capital is not a small number.
Therefore, the decision-making should be based on the measurement accuracy request of the detailed measurement point, the severity level of corrosion, the life expectancy, and the budget acceptance ability. Weigh the pros and cons, and control responsively.
If the measurement accuracy is not high. Such as for process monitoring and control. Slightly corroded, carbon steel materials can also be used for many years. After the change to stainless steel, the investment increased more. Then, it’s better to wait for the ring chamber to be corroded and unable to continue to be used. Then update the entire or damaged part of the throttling installation.
(2) Avoid the heavy
Avoiding the heavy and the light is based on a deep understanding of the process flow and the characteristics of the relevant media. Choose a measurement plan reasonably. It can also achieve the purpose of metering or stopping control of the consumption process. Avoid highly corrosive parts. And choose the less corrosive part. Even change the variety of adjusted parameters.
For example, the flow rate constant value adjustment system can be replaced by liquid level average adjustment or other suitable variable adjustment. So as to avoid the problem of corrosion resistance of flow measuring instruments.
For example, the flow of sewage into sewage treatment plants must be measured. In order to control the total discharge of pollutants. The sewage is generally acidic or alkaline. And correspondingly, an appropriate amount of alkali or acid should be added to neutralize it. Then, consider the corrosion of sewage to the flow meter. Of course, it is better to select the flow detection point after neutralization.
The flow measurement of raw gas also has a similar situation. Raw gas often contains a certain amount of sulfur dioxide. This gas is not very corrosive in boring hours. But after the wild gas is separated from the furnace. With the increase of the transfer interval. The gas temperature gradually decreases. The temperature rises accordingly. And it quickly shows condensate and is highly corrosive. When considering the location of the gas flow measuring instrument device. Of course, it should be selected before the gas presents condensate.
(3) Choose an instrument with corrosion resistance
①The instrument selection of common acid medium.
In the vortex flow sensor and turbine flow sensor, the part in contact with the fluid is acid-resistant steel. Ordinary acidic liquids and gases can be used.
The oval gear flowmeter made of acid-resistant steel can meet the needs of accurate measurement of ordinary acid liquids.
②The instrument selection of conductive liquid.
There are many kinds of lining materials for measuring tube of electromagnetic flowmeter.
Among them, the good corrosion resistance is polytetrafluoroethylene. There are also several kinds of electrode materials, which can meet the needs of most corrosive media.
When selecting electrode materials, the requirements should be met. Don’t be superstitious about precious metals. Because precious metals are not omnipotent.
Other catalysts like platinum electrodes have also attracted people’s attention. In chemical consumption, platinum is a very good catalyst. Certain media react chemically after contact with platinum under certain conditions. Proven hydrogen peroxide. The platinum electrode electromagnetic flowmeter is measuring hydrogen peroxide. Aerosol will be generated on the surface of the electrode. When the flow is zero. The output will also fluctuate.
Select appropriate electrode materials and lining materials to measure the flow of corrosive media. If the fluid temperature is also within the allowable range. That is the ideal choice, its measurement accuracy can reach 0.3~1%R.
Magnetic flowmeter can meet the needs of various measurement ranges. But if the fluid does not conduct electricity, the electromagnetic flowmeter is powerless.
③The instrument selection of non-conductive liquid.
When the clamp-on ultrasonic flowmeter works, the fluid does not directly contact the meter. Therefore, it is suitable for various corrosive fluids.
There are two types of clamp-on ultrasonic flowmeters according to their principles. Jet lag and Doppler.
The time difference method is suitable for clean single-phase fluids. The accuracy is related to pipe diameter and flow rate.
E.g:
a. When pipe diameter>150mm, v>0.3m/s, the uncertainty is ±2%R (it can reach ±1% R after calibration). v ≤0.3m/s, the uncertainty is ±O.Olm/s.
b. When the pipe diameter is ≤150mm, v>0.3m/s, the uncertainty is ±5%. v≤0.3m/s, the uncertainty is ±0.05m/s.
The Doppler flowmeter is suitable for liquids with high solid content or bubbles. The uncertainty can only reach ±1%~±10%. Obviously much lower than the electromagnetic flowmeter. Therefore, use it only when there is no other better method. The price has nothing to do with the pipe diameter. When DN≤200, ultrasonic meters are more expensive than electromagnetic flowmeters. When DN≥250, the ultrasonic flowmeter is cheaper than the electromagnetic flowmeter.
④ Selection of corrosive gas instruments
a. Ultrasonic flow meter.
In recent years, the domestic and foreign natural gas industry has achieved rapid development. This has greatly promoted the development of natural gas metering instruments. Among them, the multi-channel ultrasonic flowmeter specially developed for natural gas measurement is a dazzling pearl. If this technology is transplanted for corrosive gas flow measurement, it should be feasible. Because only the inner wall of the measuring tube needs to be treated for corrosion prevention.
b. Throttle differential pressure flowmeter.
There are no reports of commercial throttling differential pressure flow meters suitable for corrosive media. However, such meters developed by users themselves were reported decades ago.
Sino-Inst offers over 10 Magnetic Stainless Steel Flow Meter for flow measurement. About 50% of these are wastewater flow meters, 40% is the liquid flow sensor. And 20% are Ultrasonic Flow Transmitter and mass flow meter.
A wide variety of Magnetic Stainless Steel Flow Meters options are available to you, such as free samples, paid samples.
Sino-Inst is a globally recognized supplier and manufacturer of flow measurement instrumentation, located in China.
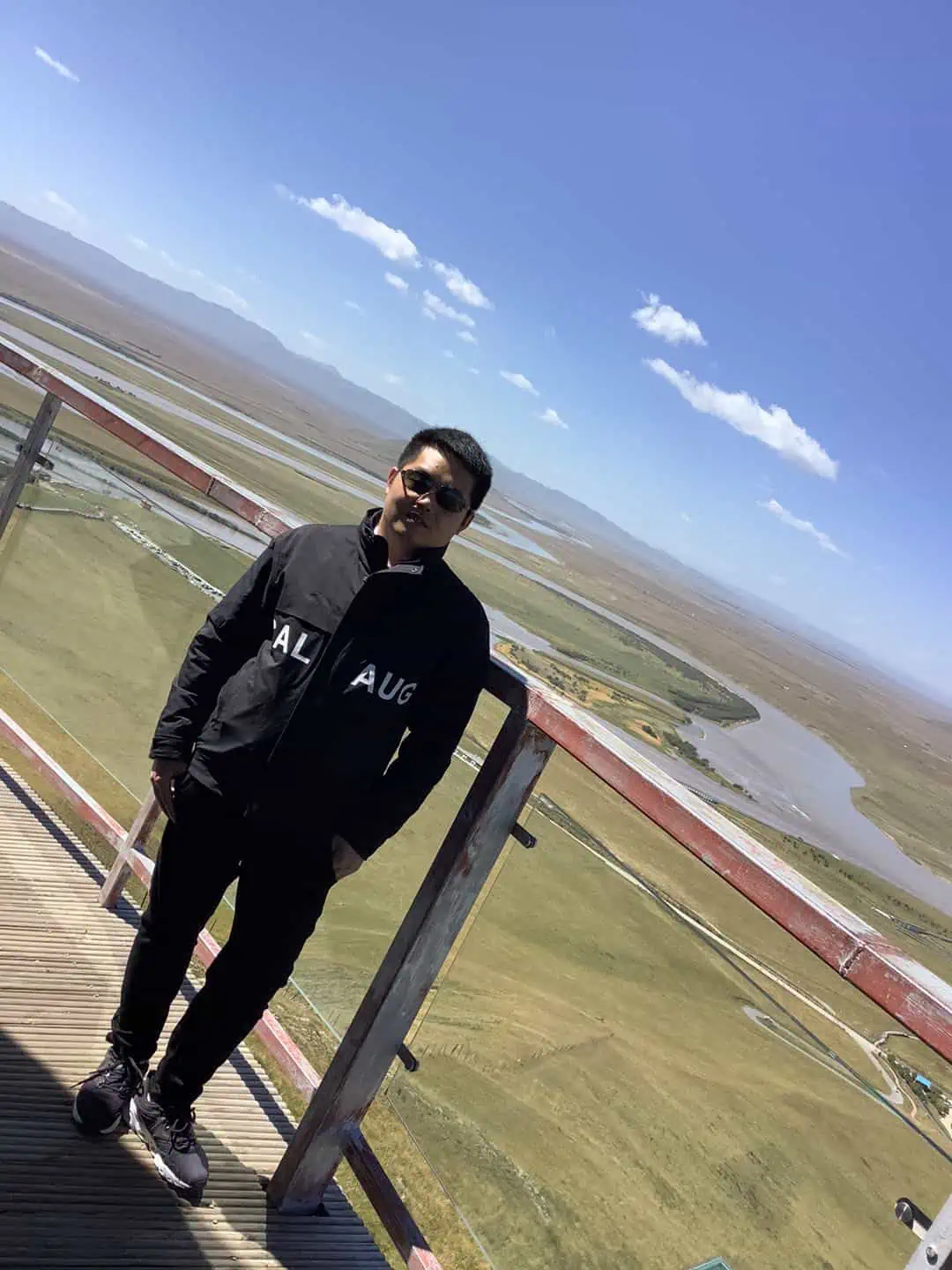
Wu Peng, born in 1980, is a highly respected and accomplished male engineer with extensive experience in the field of automation. With over 20 years of industry experience, Wu has made significant contributions to both academia and engineering projects.
Throughout his career, Wu Peng has participated in numerous national and international engineering projects. Some of his most notable projects include the development of an intelligent control system for oil refineries, the design of a cutting-edge distributed control system for petrochemical plants, and the optimization of control algorithms for natural gas pipelines.