Ammonia flow meters specifically refer to a type of flow meter that can be used to measure the flow of liquid ammonia (NH3). Ammonia flow meters ensure accurate readings and optimizing processes. Within this guide, we’ll shed light on various types, from the traditional rotometer to the advanced Gear flow meter and electromagnetic flow meters. Whether you’re dealing with liquid ammonia in an LPG setting or Gauging ammonia gas flow in specific industrial applications, understanding the intricacies of each meter—from turbine flow designs to mass flow controllers—is crucial. And while our focus is on ammonia, the principles can apply to other areas like water flow rate measurement as well. The right ammonia flow meter can significantly enhance efficiency, and in these pages, you’ll learn precisely how.
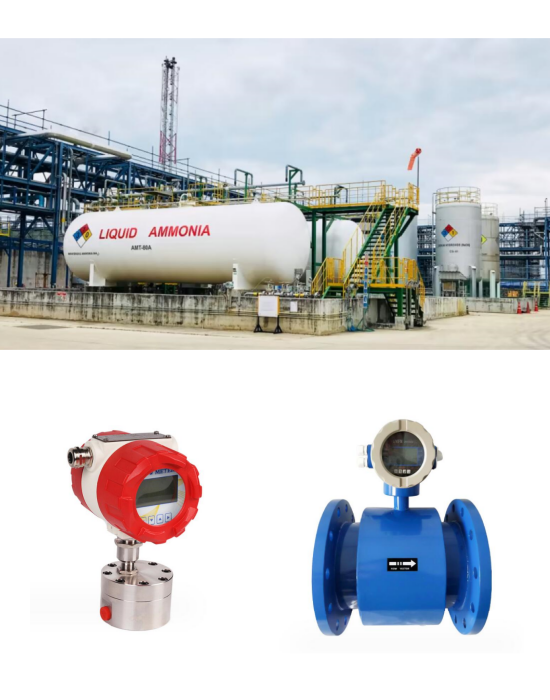
What is an Ammonia Flow Meter?
An ammonia flow meter is a specialized tool designed to measure how much ammonia—whether it’s in gas or liquid form—moves through a system. Think of it like a speedometer for your car, but instead of tracking speed, it’s tracking the flow of ammonia.
Now, why is this important? Well, in industries ranging from agriculture to manufacturing, ammonia is used for various tasks. For some, it’s crucial in refrigeration, while others might use it in the production of certain goods. To ensure everything runs smoothly and safely, these industries need to know exactly how much ammonia is flowing at any given time. That’s where the ammonia flow meter comes into play, acting as a vigilant watcher and accurate reporter of ammonia’s movement.
Characteristics of Ammonia Flow and Its Measurement Challenges
Ammonia, often recognized for its distinct, pungent smell, is a common compound in many industrial applications. However, measuring its flow isn’t as straightforward as one might hope. Let’s dive into the unique traits of ammonia and why they can make flow measurement a bit tricky.
- Dual States:
Ammonia can exist both as a gas and a liquid. The transition between these states can happen rapidly, depending on the conditions. This dual nature requires meters that can handle both forms effectively. - Reactive Nature:
Ammonia reacts with various substances, meaning it can corrode or damage certain materials. This trait means we need durable and resistant flow meters that won’t be quickly worn out by ammonia’s reactive properties. - Temperature Sensitivity:
Ammonia’s state (liquid or gas) and flow can significantly change with temperature variations. This sensitivity means measurements can fluctuate if temperatures aren’t consistent. - High Solubility in Water:
When ammonia encounters water, it dissolves quickly, leading to changes in its concentration. This solubility can complicate flow measurements, especially in environments where water presence is variable.
Challenges in Measurement:
- Material Selection: Given ammonia’s reactivity, picking the right material for the flow meter is crucial to ensure longevity and accuracy.
- Temperature Variations: Meters need to either compensate for temperature changes or work in environments with stable temperatures.
- Dual-State Monitoring: Some meters might excel in measuring liquid ammonia but struggle with its gaseous form, and vice versa. Finding a versatile tool becomes essential.
In conclusion, while ammonia is immensely useful in many industries, its unique properties present certain challenges when trying to measure its flow. But with the right tools and understanding, these challenges can be effectively managed.
Types of Ammonia Flow Meters
When diving into the intricacies of industry tools, ammonia flow meters stand out with their variety and specialized designs. Let’s explore the key meters available to measure ammonia’s flow and the pros and cons of each.
Electromagnetic Flow Meter:
- How it works: This meter creates a magnetic field. As ammonia flows through it, a voltage is produced, which is then measured to determine the flow rate.
- Advantages: No moving parts, which means less wear and tear. Suitable for various ammonia states and concentrations.
- Disadvantages: Requires a conductive fluid, so might not work best for all ammonia types.
The following is the experimental data of ammonia water conductivity:
With a concentration of 0.10%, a temperature of 15°C, and a conductivity of 2.51×10ˉ4S/cm;
With a concentration of 8.03%, a temperature of 15°C, and a conductivity of 10.38×10ˉ4S/cm;
With a concentration of 30.5%, a temperature of 15°C, and a conductivity of 1.93×10ˉ4S/cm;
According to the above data, it can be concluded that the conductivity of ammonia is greater than the minimum conductivity requirement of the electromagnetic flowmeter. Therefore, it is possible to use an electromagnetic flowmeter to measure the flow rate of ammonia water.
Ultrasonic Flow Meter:
- How it works: This meter uses sound waves to detect the rate of ammonia flow. The time it takes for these waves to travel through the fluid indicates its speed.
- Advantages: Non-invasive (no parts touch the ammonia), making it long-lasting and reducing contamination risk.
- Disadvantages: Requires a specific flow profile and can be affected by gas bubbles in the fluid.
Gear Flow Meter:
- How it works: Ammonia flows through gears in the meter. As the fluid moves, it turns the gears, and the rotations are counted to determine the flow rate.
- Advantages: Precise, especially for lower flow rates. Robust and can handle thick or viscos ammonia flows. Especially suitable for micro flow measurement. The lowest possible value is 0.6 L/H.
- Disadvantages: Moving parts can wear out and may need regular maintenance. Might not be suitable for high flow rates.
Mass Flow Meter:
- How it works: This meter directly gauges the mass of the ammonia flowing through it, rather than its volume.
- Advantages: Direct measurement without needing conversions. Accurate across a wide range of flow rates and temperatures.
- Disadvantages: Can be more expensive than other types. Might require calibration for different ammonia states or mixtures.
Picking the right ammonia flow meter is pivotal for both accuracy and durability. Knowing each type’s strengths and challenges can guide industries to the best choice for their specific needs.
How to Choose Ammonia Flow Meters
Selecting the right ammonia flow meter is a blend of science and understanding your specific needs. With a variety of meters available, how do you pinpoint the one that aligns with your industry requirements? Let’s break it down.
Desirable Features in a High-Quality Ammonia Flow Meter:
- Accuracy: A top-notch meter delivers precise readings consistently.
- Durability: Built from materials resistant to ammonia’s reactive nature, ensuring a longer lifespan.
- Versatility: Can measure ammonia in both its liquid and gaseous states effectively.
- Temperature Stability: Offers accurate measurements regardless of temperature fluctuations.
- Easy Calibration: Allows for quick adjustments based on the type of ammonia or its state.
Relevance of Features Based on Specific Industrial Applications:
For refrigeration systems, versatility is key as ammonia’s state can vary.
In chemical manufacturing, accuracy and durability might top the list to ensure correct mixtures and to withstand regular use.
For agricultural applications using anhydrous ammonia, temperature stability and easy calibration would be pivotal.
Step-by-Step Guide to Choosing Your Ammonia Flow Meter:
- Confirm media status
- Confirm pipe diameter
- Confirm flow range
- Confirm pipe pressure and pipe temperature
- Clarify measurement and control requirements. For example, what kind of signal output is required.
- Consider Cost: While quality is crucial, it’s always wise to have a budget in mind.
Remember, the perfect ammonia flow meter isn’t a universal model; it’s the one that aligns seamlessly with your specific needs and industry demands.
More Flow Measurement Solutions
Density 101: What Is the Unit of Measurement for Density
Industrial Applications of Various Density Meters
What Is a Coriolis Mass Flowmeter and How Does It Work?
Flow Measurement Units-What Is GPM in Flow Meter?
Shop Pipe Flow Meters for Liquid and Gas 101
The Pros and Cons of Micro Motion Flow Transmitters
FAQ
Navigating the world of ammonia flow meters might seem daunting at first. Yet, with the right guidance and understanding of your specific requirements, the process becomes much simpler. Remember, it’s not about the most expensive or the most advanced meter; it’s about the one that aligns perfectly with your industry and its unique demands.
When it comes to ammonia flow meters, having an experienced partner by your side makes all the difference. At Sino-Inst, we don’t just supply products – we bring years of expertise to the table. Whether you’re looking for a standard meter or seeking a customized solution, we’ve got your back. Trust in our experience, lean on our knowledge, and let’s achieve precision together.
Request a Quote
Wu Peng, born in 1980, is a highly respected and accomplished male engineer with extensive experience in the field of automation. With over 20 years of industry experience, Wu has made significant contributions to both academia and engineering projects.
Throughout his career, Wu Peng has participated in numerous national and international engineering projects. Some of his most notable projects include the development of an intelligent control system for oil refineries, the design of a cutting-edge distributed control system for petrochemical plants, and the optimization of control algorithms for natural gas pipelines.