What Is the Ultrasonic CO2 Level Indicator?
Ultrasonic CO2 Level Indicator is the best CO2 Bottle Level Measuring Device. Our product Portable Ultrasonic Liquid Level Indicator can effectively detect the storage capacity of the fire extinguishing agent storage container in the gas fire extinguishing system (such as: Proto-Indo-European, halo-alkane, CO2, etc.).
Our Portable Ultrasonic Liquid Level Indicator uses non-contact detection technology and is ideal for detecting hazardous toxic or corrosive liquids. It can be used to measure whether there is liquid at a certain height in a container or pipeline.
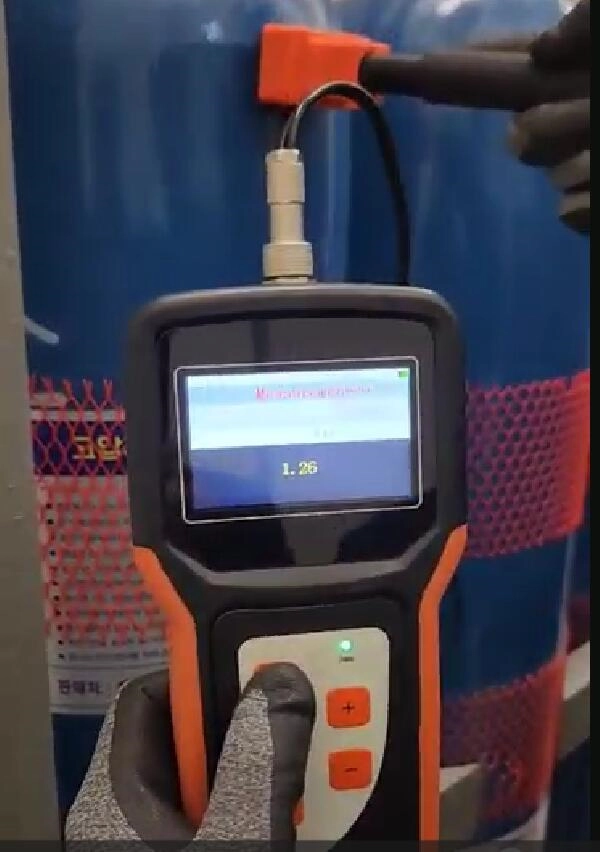
Portable Ultrasonic Level Indicator
Our Portable Ultrasonic Liquid Level Indicator for tank is designed to determine the presence or absence of the liquid at a certain height in a container or in pipeline. The liquid containers to be measured can be made of various kinds of materials such as metal, glass or un-foamed plastics.
Under ordinary conditions, the maximum wall thickness of measured containers is 30mm. The indicator can be used to detect various types of liquids (without crystallization or other particulate matter). Because of the innovative non-contact detection methods, this liquid level indicator is an ideal choice for the detecting dangerous toxic or corrosive liquids.
Features
- No physical contact with medium
- Suitable for toxic, corrosive, or invasive media
- No need for drilling or welding on tank wall
- Simple and convenient to operate and maintain
- Ultrasonic adaptive detection algorithm.
- High-contrast OLED color display, suitable for outdoor use under strong light
- Intuitive user interface design
- Comprehensive software displays measurements simply and clearly
Applicable CO2 Tanks/Cylinders/Bottles
CO2 Tank with any of the following diameter ranges:
210mm-230mm, 265mm-285mm, 340mm-360mm, 390mm-410mm
Common Tank:
All tanks outside the above tank diameter ranges can be considered as common type.
vertical tank / horizontal tank / spherical tank(diameter <3M)
The indicator has no requirement towards medium, height and pressure.
Parameters
Measurement accuracy | < 5mm |
Measurable range of wall thickness | 3~30 mm |
Measurable tank material | Steel, stainless steel, glass, unformed plastics |
Measurable medium | Pure liquid, milky liquid, suspension liquid |
Ambient temperature | -20℃〜60℃ (-4℉〜+140℉) |
Ambient humidity | 15% ~ 85% RH |
Power supply | Two lithium batteries (supplied by customers) |
Current | 100 mAh (on average) |
Ultrasonic CO2 Level Indicator CO2 Tank Measurement
CO2 cylinder specifications (external diameter division):
The CO2 cylinders measured by this meter are divided into the following 4 specifications:
215mm-225mm diameter cylinders,
270mm-280mm diameter cylinders,
345mm-355mm diameter cylinders,
395mm-405mm diameter cylinders.
There are no excessive requirements for the height of the medium and the tank.
CO2 cylinder measurement operation:
- Select “co2 cylinder”-“Choose a suitable cylinder diameter” through the menu and enter the measurement interface.
- Hold the probe vertically and tightly on the tank, and press the button to measure.
- Measurement results are based on measurement parameters and level indicator lights (red is “no liquid”, green is “with liquid”)
- Generally, the measurement is started from the bottom of the storage tank (measurement with liquid position). If the measurement parameter is> = 2, the current level is considered to be a liquid-free position, and <2 is considered to be a liquid level; if it is floatingaround 2, It is considered that the liquid level of the horizontal plane is approaching the liquid surface (usually about 5 cm).
- Take multiple points on the same horizontal plane for measurement, and take the result with the highest probability as the final result (avoid the interference of welds and unknown factors).
- Find the liquid level position step by step through theapproximation measurement.
CO2 cylinder measurement Note:
Due to the irregular air outlet and a large number of welding kits at the top of the co2 cylinder, the measurement results at the bottom and top are invalid. (The top is generally empty in the case of a full tank).
Please refer to the video below to understand the operation tutorial and case of Ultrasonic CO2 Level Indicator.
In addition to Ultrasonic CO2 Level Indicator, we have more applications of ultrasonic technology.
More Ultrasonic Prodcuts
Our Sino-inst Ultrasonic CO2 Level Indicator stands as a symbol of safety, precision, and efficiency in industrial applications. This superior device excels in assessing fire extinguishing systems, accurately measuring storage capacity with its non-contact det ection technology. It is versatile, handling various agents like Proto-Indo-European, halo-alkane, and CO2.
The safety advantages of this tool are unmatched, as it ensures no direct contact with toxic or corrosive liquids. Industries that prioritize safety, accuracy, and reliability find enormous value in our Ultrasonic CO2 Level Indicator. Whether for regular monitoring or spot checks, it provides dependable data, ensuring operations run smoothly and safely. Trust the Ultrasonic CO2 Level Indicator – it’s your partner in precision.
Our Ultrasonic CO2 Level Indicator is widely sold to various countries in the world. As an excellent and portable CO2 Bottle Level Measuring Device, it provides convenience for various industries such as fire protection. If you need, please feel free to contact Sino-Inst!
Request a Quote
Wu Peng, born in 1980, is a highly respected and accomplished male engineer with extensive experience in the field of automation. With over 20 years of industry experience, Wu has made significant contributions to both academia and engineering projects.
Throughout his career, Wu Peng has participated in numerous national and international engineering projects. Some of his most notable projects include the development of an intelligent control system for oil refineries, the design of a cutting-edge distributed control system for petrochemical plants, and the optimization of control algorithms for natural gas pipelines.