A liquid flow meter is an instrument designed to measure the volume or mass of a liquid flowing through a pipe. It plays a vital role in ensuring the efficiency and accuracy of industrial processes. From managing water supply in municipalities to controlling processes in the food and beverage industry, liquid flow meters are ubiquitous. With a variety of types and designs, each with its unique features, the perfect liquid flow meter can greatly enhance your operation.
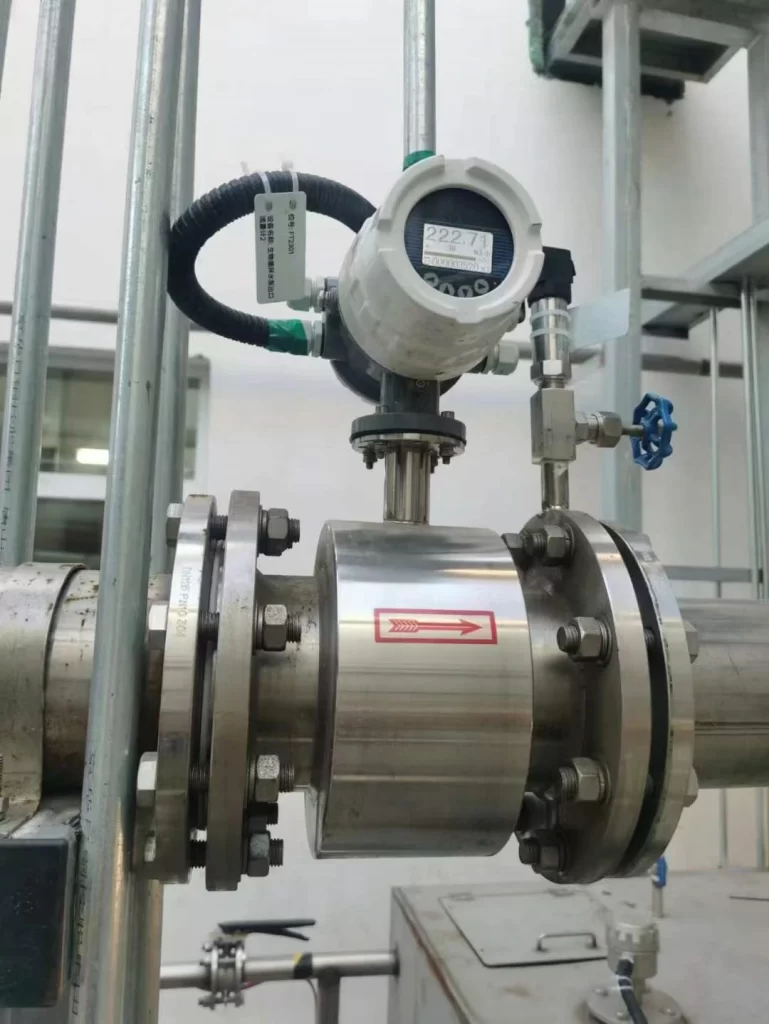
Top Liquid Flow Meters in Industry
At Sino-Inst, we provide liquid flow meters that make tracking the flow rates of various liquids a breeze. From water and fuels to thicker fluids, our meters are designed for ease and accuracy. Whether you need a meter for non-drinking water, fuel-dispensing pumps, or industrial flow measurement, we’ve got you covered.
We offer a broad selection of liquid flow meters, perfect for managing water, petroleum products, fuels, and chemicals.
In short, if you’re searching for a fluid flow meter that’s just right for measuring liquid flow, Sino-Inst is the place to look. We’re here to make liquid flow measurement straightforward and hassle-free.
Types of Liquid Flow Meters
Liquid flow meters come in many shapes and sizes, each built for a specific use. Here are some common types:
Electromagnetic Flow Meters: These meters use a magnetic field to measure flow. They’re great for liquids like water, as they’re clean, accurate, and don’t block the flow.
Turbine Flow Meters: These meters have a little wheel, or “turbine,” that spins when liquid flows past. The faster the liquid, the faster the turbine spins, giving a measure of the flow rate.
Ultrasonic Flow Meters: These meters use sound waves to figure out the speed of the liquid. They are perfect for jobs where you don’t want to touch the liquid you’re measuring.
Mass Flow Meters: These meters are a bit like a tiny weighing scale. They measure the actual mass of the liquid, not just the volume. These are often used in chemical processes.
Positive Displacement (Gear) Meters: Think of these like a water wheel in a stream. As the liquid flows, it turns gears. The number of turns tells you the flow rate. They are very precise and can be used with a wide range of liquids.
Differential Pressure (DP) Flow Meters: These clever devices measure the drop in pressure across a restriction to calculate flow rate. They’re robust, reliable, and can handle a wide variety of conditions.
Remember, each type of flow meter is good at specific tasks. The key is to match the right meter to your needs.
Choosing the Right Liquid Flow Meter
Choosing the right flow meter is crucial for the success of your operation. Factors to consider include:
- Accuracy: Some applications may require very accurate measurements, while others can afford a bit of error.
- Cost: The total cost of ownership, including the initial cost, installation, and maintenance costs, should be considered.
- Ease of Installation and Maintenance: Some meters, like the clamp-on flow meters, are easier to install and maintain than others.
- Pipe Size: The size of the pipe in which the meter will be installed is a crucial factor. For example, a 1″ water flow meter may be suitable for some applications but not for others.
FAQ
More Flow Measurement Solutions
Flow Meter Selection Guide 101: Find the Perfect Fit for Your Application
Top Industrial Heating Oil Flow Meters
Condensate Flow Meter-Steam Condensate Flow Meter|Types & Selection Guide
Air Flow Measurement Instruments for Industrial Harsh Conditions
Top Flow Meters for PVC Pipes: Find Your Ideal Match
Shop Pipe Flow Meters for Liquid and Gas 101
Choosing the right liquid flow meter can greatly enhance your operation’s efficiency and accuracy. By understanding the features and benefits of different flow meters, you can make an informed decision and select the best meter for your specific application.
At Sino-Inst, we are experienced manufacturers and suppliers of a wide range of liquid flow meters. With our expertise and extensive selection, we can help you find the perfect flow meter for your needs.
Request a Quote
Wu Peng, born in 1980, is a highly respected and accomplished male engineer with extensive experience in the field of automation. With over 20 years of industry experience, Wu has made significant contributions to both academia and engineering projects.
Throughout his career, Wu Peng has participated in numerous national and international engineering projects. Some of his most notable projects include the development of an intelligent control system for oil refineries, the design of a cutting-edge distributed control system for petrochemical plants, and the optimization of control algorithms for natural gas pipelines.