What is a capacitive liquid level sensors?
Capacitive liquid level sensor is an instrument for continuous measurement of liquids and converting it to an electrical signal.
Capacitive liquid level sensors play a pivotal role in obtaining precise, continuous measurements of liquids within containers. Being versatile enough to work seamlessly with fuels, oils, water, and coolant fluids. At its core, this sensor gauges the liquid’s height and transforms that data into an electrical signal. This valuable signal can then interface with various instruments, enabling users to visualize, monitor, record, or manage the liquid’s level.
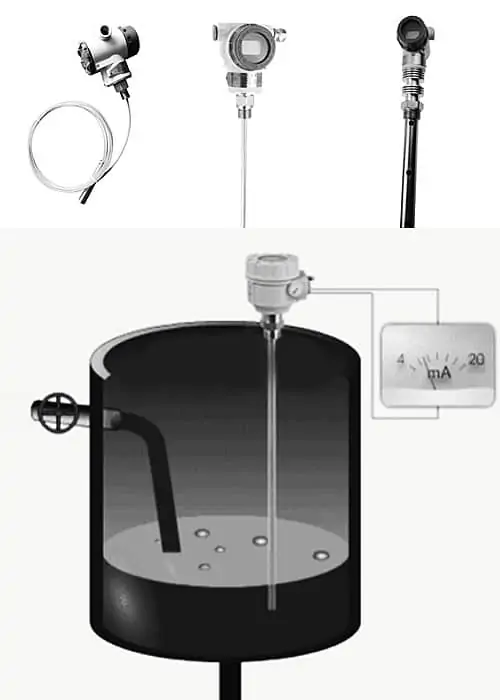
Capacitive liquid level sensor with good structure and installation method can be applied to high temperature, high pressure, strong corrosion, easy to crystallize, anti-clogging, anti-freezing, and solid powder and granular materials.
Sino-Inst’s capacitive liquid level sensor can measure the liquid level of a highly corrosive medium. It measures the liquid level of a high-temperature medium. It measures the liquid level of sealed containers. It has nothing to do with the viscosity, density, and working pressure of the medium.
Features of capacitive liquid level sensors
Extended reading: Radar Non Contact Water Level Sensor
Capacitive liquid level sensors types
Extended Reading: How to Measure Volume of Liquid
How does a capacitive liquid level sensor work?
Define capacitor
What is a Capacitor?
A capacitor is a passive electronic component that stores and releases electrical energy. In its most basic form, a capacitor consists of two conductive plates separated by an insulating material known as a dielectric.
When voltage is applied to the plates, an electric field forms, causing positive and negative charges to accumulate on the plates.
This stored energy can later be discharged when needed. The capability of a capacitor to store energy is measured in Farads (F) and is referred to as its capacitance.
Connection Between a Capacitor and a Capacitive Liquid Level Sensor:
The principle behind a Capacitive Liquid Level Sensor is intrinsically tied to the concept of capacitance. Here’s how they relate:
Formation of a Capacitor:
In the context of a capacitive liquid level sensor, the probe (or immersed electrode) acts as one plate of the capacitor, and the opposing electrode (often the container or tank wall) serves as the other plate.
Role of the Liquid (Dielectric):
The liquid whose level is being measured acts as the dielectric medium in this capacitor setup. Different liquids have different dielectric constants, which can affect the capacitance.
Changing Capacitance:
As the level of the liquid changes, the portion of the probe submerged in the liquid varies. This changes the effective dielectric between the capacitor plates, leading to a change in capacitance. This variation in capacitance is directly proportional to the level of the liquid.
Measurement Principle:
The electronics in the sensor detect these changes in capacitance. By monitoring these changes, the sensor can determine the liquid’s level and convert it into a readable signal.
While a capacitor is a foundational component in electronics for energy storage, the principle of capacitance is what allows a Capacitive Liquid Level Sensor to function. The sensor effectively creates a dynamic capacitor whose properties change based on the liquid’s level, making it an ingenious application of basic electronic principles to real-world measurement challenges.
Capacitive liquid level sensor working principle
The Capacitive liquid level sensor is used to measure the change of capacitance to measure the level of the liquid level. The capacitive liquid level sensor is used to measure the change of capacitance to measure the unevenness of the liquid level.
The capacitive liquid level sensor is a metal rod pierced into the liquid container. The metal rod serves as a pole of the capacitor. The container wall serves as the other pole of the capacitor. The medium between the two electrodes is the liquid and the gas above it.
Because the dielectric constant ε1 of the liquid is different from the dielectric constant ε2 on the liquid surface. For example ε1>ε2.
Then when the liquid level rises, the total dielectric constant between the two electrodes of the capacitive liquid level gauge increases accordingly, so the capacitance increases.
Conversely, when the liquid level drops, the value of ε decreases and the capacitance also decreases.
Therefore, the Capacitive liquid level sensor can measure the unevenness of the liquid level by changing the capacitance between the two electrodes. The sensitivity of the Capacitive liquid level sensor mainly depends on the difference between the two dielectric constants.
Moreover, as long as ε1 and ε2 are stable, the liquid level measurement is accurate. Because the measured medium has conductivity. Therefore, the metal rod electrode is covered by an insulating layer.
The capacitive liquid level sensor is small in size, simple to complete remote transmission and scheduling, suitable for liquid level measurement of corrosive and high-pressure media.
Extended Reading: GWR Level Sensor for High Temperature & High Pressure
Let’s watch a video. It will help you understand the working principle of the capacitive liquid level sensor.
Video source: https://www.youtube.com/watch?v=0du-QU1Q0T4
Extended reading: Non-Contact Level Measurement
Advantages of Capacitance Level Sensors:
- Versatility: These sensors perform well with various dielectric fluids, making them suitable for a wide range of applications.
- Durability: Their robust design, often using stainless steel, means they are resistant to most fluids and harsh conditions. This ensures a long service life.
- No Moving Parts: Their absence of moving components ensures they require minimal maintenance, which is particularly advantageous in challenging environments.
- High-Temperature Compatibility: Since they don’t have sensitive components submerged in the liquid, they can operate in hotter fluids where some other sensors might struggle.
- Sealed System Compatibility: Their design allows them to function efficiently in sealed pressurized or evacuated vessels without any significant impact on performance.
- Simplicity: With a straightforward mechanical structure, they are less prone to mechanical breakdowns.
Disadvantages of Capacitance Level Sensors:
- Conductive Fluid Limitation: These sensors might face challenges with conductive fluids unless they come with an insulated outer tube.
- Coating Issues: Thick or sticky media might coat the probe, creating an insulation layer that can lead to malfunctions or compromised performance.
- Calibration Necessity: They require calibration to distinguish the difference between liquid and air accurately. This might need occasional recalibration based on the medium.
- Dielectric Constant Sensitivity: Changes in the medium that cause the dielectric constant to shift can impact the sensor’s performance.
- Possible Obstruction: The probe might protrude into the liquid, causing obstruction, attracting fouling, or even raising hygiene concerns in certain applications.
Capacitive level sensor Applications
The capacitive liquid level sensor is used to measure the liquid level (level) of conductive and non-conductive liquids (solids) under pressure in pressure vessels.
A capacitive liquid level sensor can convert the changes of various liquid level parameters into standard current signals. Remote transmission to the operating room. For the secondary instrument or computer device for centralized display, start emergency signal or automatic control.
Combine the user’s specific process conditions, equipment structure, and use requirements. Through the flexible combination of the material, structure, and installation method of the level gauge. It is suitable for continuous detection of liquid level, material level or material level under special conditions such as high pressure, high temperature, strong corrosion, easy crystallization, anti-blocking, anti-freezing, and solid powder and granular materials. It can be widely used in detection and control in various industrial processes.
Capacitive level sensor application:
- Conductive, insulating liquid-chemical industry, oil field, water and sewage treatment
- Conductive and insulating slurry-papermaking, pharmaceutical, water and sewage treatment
- Powder, ash, powder-power plant, metallurgy, cement
- Pellets, coal, grain-power plants, metallurgy, grain
- Interface, two different liquids-oil field, chemical industry
Extended reading: Radar Liquid Level Sensor|Corrosive, steam, volatile liquids
Extended reading: Radar Water Level Sensor Applications
Capacitive oil level sensor
The capacitive fuel level sensor refers to a capacitive liquid level transmitter used to measure the oil level. According to the principle of capacitance sensing, when the height of the measured electrode dips and changes, the capacitance of the measured electrode changes. It can convert the change of oil level into a standard current signal. It is remotely transmitted to the operation control room for the secondary instrument or computer device for centralized display, alarm, or automatic control.
Read more about Capacitive Fuel Level Sensor
Extended Reading: Low Cost Float Level Sensor for Tank Liquid Volume Monitoring
Capacitive sensor for water level measurement
A capacitive water level sensor is often used to measure the water level of the water storage tank. The capacitive water level sensor uses the change of measuring capacitance value to measure the height of the liquid level. The main function is to continuously measure the liquid level of the measured medium liquid. For example, common media are sewage, mud, paper pulp, eight-treasure porridge, and so on. You may also have heard of a non-contact capacitive water level sensor. It is a kind of capacitive water level sensor installed externally.
Read More about Contact and Non-contact | Capacitive water level sensor
Read more about: Hydrostatic Submersible Level Transmitter-Straight Rod Insertion
Capacitive level switch
The principle of a Capacitive level switch is a position sensor with switch output.
The capacitive level switch is composed of an electronic circuit module unit and sensor rod. The induction pole and the barrel wall are used as the two electrodes of the capacitor.
When the material between the two electrodes changes, the capacitance value changes. After the electronic circuit unit detects this capacitance value change. The analysis and processing unit are compared with the set capacitance value. When it is higher than the set value, a switch signal is an output.
It is widely used for position detection in various high temperature, high pressure, strong acid and strong alkali, and various powder and particle environments in petroleum, chemical, metallurgical, light industry, coal, cement, grain, and other industries.
Extended reading: Diesel fuel tank level gauges & indicators
Extended Reading: What is level transmitter working principle?
Extended reading: Ultrasonic liquid level sensors
More Featured Level Senors
Extended reading: Ultrasonic level transmitter for Hazardous Liquids
Related Blog
Extended reading: Corrosive Liquid Chemical Level Sensor in Chemical Processing
Sino-Inst offers over 10 Capacitive Level Sensors for level measurement. About 50% of these are RF level meters, 40% is the tank level sensor.
A wide variety of Capacitive Level Sensors are available to you, such as free samples, paid samples.
Sino-Inst is a globally recognized supplier and manufacturer of Capacitive Level measurement instrumentation, located in China.
Request a Quote
Wu Peng, born in 1980, is a highly respected and accomplished male engineer with extensive experience in the field of automation. With over 20 years of industry experience, Wu has made significant contributions to both academia and engineering projects.
Throughout his career, Wu Peng has participated in numerous national and international engineering projects. Some of his most notable projects include the development of an intelligent control system for oil refineries, the design of a cutting-edge distributed control system for petrochemical plants, and the optimization of control algorithms for natural gas pipelines.