Pulse flow meters stand as a paragon of modern flow measurement technology. Pulse signals, often relayed to devices like PLCs as input data, help industries measure and manage flow with unparalleled precision. While many might be familiar with the traditional water meter or turbine flow transmitter, the evolution of flow measurement technology has introduced sophisticated devices such as the electromagnetic flow meters and dual pulse systems. The role of pulse signals, especially in devices like the turbine flowmeter, is crucial. It ensures the accurate translation of magnetic flow into actionable data, transforming how industries monitor and optimize their operations.
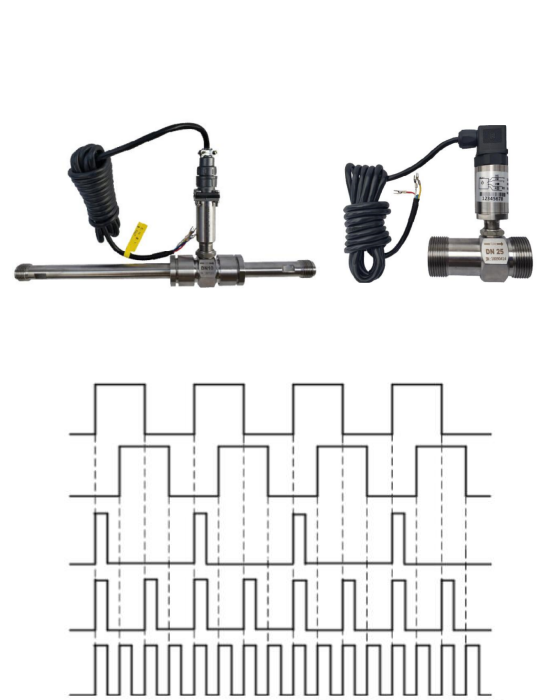
Featured Pulse Flow Meters
what is pulse output signal?
A pulse output signal is an integral facet of modern flow measurement. Essentially, it is a series of electronic pulses generated each time a specific volume of fluid, such as water, passes through a meter. Think of it as the flow meter’s heartbeat, where every pulse equates to a predetermined volume of fluid.
The mechanics behind this are quite fascinating. Within many flow meters, such as turbine flowmeters, the fluid’s movement causes an internal rotor to turn. As this rotor spins, it interacts with sensors—often magnetic ones. Each interaction results in the generation of an electronic pulse. The number of these pulses directly corresponds to the volume of fluid that has passed through the meter. This real-time pulsating data representation is invaluable as it grants accurate, instantaneous measurements, making data interpretation and integration seamless in various systems.
Pulse Output vs 4-20mA
When diving into the world of flow measurements and signal outputs, a frequent comparison arises between pulse output and the traditional 4-20mA signal.
The 4-20mA signal is a staple in analog devices, providing a continuous current signal that correlates to the measurement variable. On the flip side, pulse output offers discrete, distinct signals.
While both pulse output and 4-20mA signals have their unique strengths, the digital character of pulse outputs typically allows for more precise data. This is especially true in applications that demand rapid response or detailed flow analysis. In essence, while 4-20mA signals give a continuous overview, pulse outputs provide granular, moment-by-moment insights, leading to a richer understanding of flow dynamics.
Pulse Flow vs. Continuous Flow
In the world of flow measurement, two prominent types emerge: pulse flow and continuous flow. Understanding their distinctions is pivotal for industries aiming to optimize their fluid management processes.
Pulse Flow Meters:
Pulse flow meters, as the name suggests, measure flow using a pulsating technique. With every predefined volume of fluid that passes through, the meter emits an electronic pulse. This digital representation makes it ideal for applications requiring precision and rapid data collection.
Key Features of Pulse Flow Meters:
- Real-time Data: These meters provide instantaneous measurements, giving an up-to-the-moment view of flow rates.
- Digital Precision: As they operate based on discrete pulses, they can offer granular data, capturing even minor fluctuations in flow.
- Versatility: Pulse flow meters can be integrated into various systems, making them suitable for diverse applications.
Continuous Flow Meters:
On the other hand, continuous flow meters offer a steady, uninterrupted measurement of fluid flow. Instead of discrete pulses, they provide a continuous analog signal, representing the flow rate over a period.
Key Features of Continuous Flow Meters:
- Consistent Monitoring: These meters are excellent for applications where continuous monitoring is essential, providing a holistic view of flow dynamics.
- Analog Output: They typically use signals like 4-20mA, offering a smooth data curve over time.
- Broad Range: Continuous flow meters can capture a wide range of flow rates, making them versatile for varied applications.
In Conclusion:
Choosing between pulse and continuous flow meters boils down to the specific needs of an application. Pulse flow meters shine in scenarios demanding detailed, real-time data. In contrast, continuous flow meters are the go-to for holistic, round-the-clock monitoring. By understanding their core differences, industries can make informed decisions, ensuring optimal flow management.
Pulse Flow Meter Working Principle
The Core Principle:
At its essence, a pulse flow meter operates by translating the flow of fluid into electronic pulses. Think of these pulses as the meter’s heartbeat, with each beat or pulse representing a specific volume of fluid that has flowed through the meter.
How It Works:
- Fluid Interaction: As fluid (be it water, oil, or any other liquid) passes through the meter, it interacts with a mechanism inside, often a rotor or a turbine.
- Rotor Movement: This fluid movement causes the rotor to spin. The speed of this rotation correlates directly with the flow rate of the fluid.
- Sensing the Rotation: Surrounding this rotor are sensors, usually of a magnetic nature. Each time the rotor completes a specific rotation or passes a point, it triggers these sensors.
- Pulse Generation: Every trigger from the rotor to the sensor results in the creation of an electronic pulse. This is relayed as an output from the flow meter.
- Data Interpretation: The number of pulses over time gives a precise measure of the volume of fluid that has passed through. The faster the fluid flow, the quicker the pulses are generated.
Why Pulse Signals Matter:
Pulse signals offer a clear advantage – digital precision. Unlike analog signals that provide a continuous representation, pulse signals give a moment-by-moment account of flow, making data interpretation straightforward and accurate.
Flow Meter Pulse Output to PLC: A Seamless Integration for Precision
In the landscape of industrial automation, the synergy between devices can be the linchpin of operational efficiency. A prime example of this is the integration of flow meters, specifically their pulse outputs, with Programmable Logic Controllers (PLCs). Let’s explore this integration and its significance.
In essence, when fluid passes through a flow meter, it results in the generation of electronic pulses. Each pulse represents a specific volume of the fluid, offering a digital snapshot of the flow rate.
PLCs serve as the brains behind many automated systems. They accept inputs from various devices, process this data based on programmed logic, and then generate outputs to control equipment or processes.
The Integration Process:
- Signal Transmission: The flow meter generates pulse outputs based on fluid flow. These pulses are then transmitted as electrical signals to the PLC.
- Data Interpretation: Upon receiving the signals, the PLC interprets the frequency of pulses to determine the flow rate. The higher the frequency, the greater the flow.
- Actionable Outputs: Based on the interpreted data and the logic programmed into the PLC, decisions are made. This can range from adjusting valves, triggering alarms, or even integrating with broader systems for holistic process control.
Benefits of Integration:
- Real-time Control: By continuously monitoring flow rates, PLCs can make instant adjustments, ensuring optimal operations.
- Data Accuracy: The digital nature of pulse outputs ensures precision, leading to accurate and reliable PLC actions.
- System Flexibility: The ability to program PLCs means that as system requirements change, adjustments can be made without altering the physical infrastructure.
The integration of flow meter pulse outputs with PLCs exemplifies the power of modern automation. This seamless synergy offers industries a reliable, flexible, and precise method to monitor and control fluid flow, driving efficiency and accuracy in operations. By understanding this integration, professionals can better harness the potential of their systems, leading to superior outcomes.
Applications of Pulse Flow Meters Across Industries
Pulse flow meters, with their unique ability to capture flow data through electronic pulses, have become an invaluable tool in various industries.
- Manufacturing:
In the vast world of manufacturing, maintaining a consistent and accurate flow of liquids—whether it’s raw materials, coolants, or finished products—is paramount. Pulse flow meters offer real-time monitoring, allowing industries to maintain product quality, ensure safety, and optimize processes. - Pharmaceuticals:
Accuracy is non-negotiable in the pharmaceutical industry. When formulating medications, precise quantities of liquid ingredients need to be mixed. Pulse flow meters ensure that these formulations are consistent, safeguarding the efficacy and safety of medical products. - Energy & Power Generation:
In power plants, especially those relying on liquid fuels or coolants, monitoring flow is critical. Pulse flow meters track the rate of fuel consumption or coolant flow, enabling plants to optimize operations and reduce wastage. - Agriculture:
Modern agriculture heavily relies on irrigation systems. Pulse flow meters help farmers measure the flow of water, ensuring crops receive the right amount, neither too little nor too much. - Water Treatment:
In water treatment plants, accurate flow measurement is key for processes like filtration and chemical treatment. Pulse flow meters provide reliable data, ensuring water quality and efficient treatment. - Food & Beverage:
Whether it’s brewing beer or producing dairy products, the flow of liquids is at the core of the food and beverage industry. These meters ensure consistency in production, guaranteeing that every bottle, carton, or can meets quality standards. - Chemical Processing:
In chemical plants, reactions often require exact quantities of liquid reactants. Pulse flow meters allow for precision, ensuring desired outcomes and minimizing risks.
More Flow Measurement Solutions
Flow Meter Straight Length Requirements Guide
What Is Density Flow Meter: Principles and Applications
What Is a Turbine Flow Meter for Gas? and Why Choose It?
The Role of Gear Flow Meters For Cement Additives
Buyer’s Guide to Industrial Fertilizer Flow Meters
What is an Ammonia Flow Meter and How to Choose?
FAQ
From everyday products to specialized applications, pulse flow meters play a silent yet significant role. They stand as guardians of quality, efficiency, and safety across industries. Recognizing their applications allows professionals to better utilize them, driving innovation and precision in their respective sectors.
But flow measurement doesn’t stop at pulses. From crude oil flow measurement, ensuring the smooth operation of our energy sectors, to liquid level measurement, vital for reservoirs, tanks, and storage facilities. Moreover, the precise temperature measurement instruments play a crucial role, especially in industries where slight temperature variances can impact product quality or safety.
With a rich legacy in the field, Sino-Inst stands at the forefront of measurement technology. As an experienced manufacturer and supplier, our portfolio extends beyond pulse flow meters. Whether you need customized solutions or off-the-shelf instruments, our team is ready to assist, ensuring you have the right tools for your unique requirements.
Request a Quote
Wu Peng, born in 1980, is a highly respected and accomplished male engineer with extensive experience in the field of automation. With over 20 years of industry experience, Wu has made significant contributions to both academia and engineering projects.
Throughout his career, Wu Peng has participated in numerous national and international engineering projects. Some of his most notable projects include the development of an intelligent control system for oil refineries, the design of a cutting-edge distributed control system for petrochemical plants, and the optimization of control algorithms for natural gas pipelines.