Liquid Level Sensor Probes are an essential part of liquid level transmitters. When purchasing a liquid level meter, we must consider the type of Liquid Level Sensor Probes, such as contact or non-contact. Such as the length of the probe, capacitive probe, float probe rod, etc. Or the working principle of Liquid Level Sensor Probes, such as ultrasonic, radar, hydrostatic pressure, etc. Selecting the right type is crucial, as it ensures accuracy, efficiency, and the reliability of the measurement. Whether in industries like food processing, oil and gas, or water treatment, the right sensor can optimize operations and minimize risks.
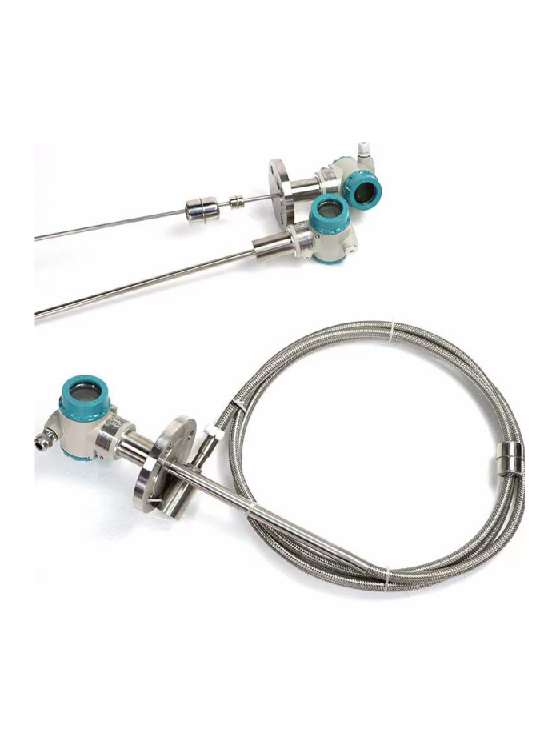
What is Liquid Level Sensor Probe?
We can understand that a level meter is composed of a probe and a transmitter. Liquid Level Sensor Probes detect the amount of liquid in a specific space, like a tank or a bottle. They’re vital because they help monitor and control the amount of liquid, making sure there’s not too much or too little. This control keeps systems running smoothly and safely, saving both time and money.
For example, Capacitance sensing probe devices for measuring liquid level and converting it to an electrical signal to send to other instrumentation.
You may also have seen straight rod probes, cable probes, and coaxial probes. Or PTFE non-contact probe. Then, according to our many years of experience, Liquid Level Sensor Probes can be classified from several aspects. That is: working principle and material.
From the material point of view, it is easy to understand. It only needs to be compatible with the measured liquid. For example, to measure sulfuric acid, the probe is generally made of anti-corrosion material, such as PTFE. Therefore, when we select enough level meters, we only need to inform the manufacturer of the compatible materials of the measured medium.
Next, let’s look at different types of Liquid Level Sensor Probes from the working principle.
Types of Liquid Level Sensor Probes
Float Level Sensor Probes
Float Level Sensors are widely used in applications where accurate liquid level measurements are needed. Common scenarios include water tanks, where they help in maintaining the desired water level; fuel systems, to monitor fuel storage; sump pumps, to prevent flooding.
Their simplicity and reliability make them suitable for many liquid monitoring tasks.
Advantages:
- Simple Design: Easy to install and use.
- Cost-Effective: Suitable for budget-conscious applications.
- Reliable: Performs well in various standard applications.
- It can be made into a multi-float form. For multi-level control.
Disadvantages:
- Limited Use: Not suitable for turbulent or dirty liquids.
- Wear and Tear: Moving parts may require regular maintenance.
Capacitive Liquid Level Sensor Probes
Capacitive Liquid Level Sensor Probes work on the principle of detecting changes in electrical capacitance caused by the presence of a liquid. The sensor probe forms one plate of a capacitor, and the liquid acts as a dielectric material. Changes in the level of the liquid alter the capacitance, providing a measure of the liquid’s level.
Typical applications include the food and beverage industry, pharmaceuticals, and chemical processing, where non-contact, versatile liquid level sensing is needed, particularly with non-conductive or high-temperature fluids.
Advantages:
- Works Well on Dielectric Fluids.
- Simple Mechanical Construction: Easy to manufacture and install.
- No Moving Parts: This reduces the need for regular inspection and maintenance, and minimizes wear and tear.
- High-Temperature Fluid Compatibility: Since no sensitive components make contact with the fluid, it can handle high temperatures.
- Performance Unaffected in Sealed or Pressurized Vessels: The design ensures stable functioning in different container types.
Disadvantages:
- Incompatibility with Conductive Fluids: Requires an insulated outer tube for working with conductive liquids.
- Issues with Thick or Sticky Media: Such substances can coat the probe, creating an insulation layer that causes malfunction or affects performance.
- Requires Calibration: Proper setup is needed to distinguish between liquid and air.
- Sensitive to Changes in Media: Changes in the dielectric constant of the fluid can affect readings.
- Potential Obstruction and Cleanliness Issues: Probe protruding into the liquid might cause blockage, attract fouling, and create hygiene concerns.
Ultrasonic Level Sensor Probes
Ultrasonic Level Sensor Probes function by emitting sound waves at ultrasonic frequencies. These waves bounce off the surface of the liquid and are detected by the sensor. By calculating the time taken for the sound waves to return, the distance to the liquid surface, and hence the level, is determined.
Ultrasonic sensors are commonly used in wastewater treatment, oil and gas industries, and irrigation systems, where non-contact measurement is preferred. Their capability to work with dirty or corrosive liquids makes them valuable in such applications.
Advantages:
- Non-Contact Measurement: Suitable for corrosive or dirty liquids.
- High Accuracy: Provides precise readings.
- Versatile: Works well in various conditions. Such as explosion-proof.
Disadvantages:
- Sensitive to Foam or Vapor: These factors may affect performance.
- Measuring distance is limited. Ultrasonic is not suitable for larger measuring ranges.
Radar Level Sensor Probes
Radar Level Sensor Probes operate using radio waves. A radar pulse is transmitted, which reflects off the surface of the liquid and returns to the sensor. By measuring the time it takes for the pulse to travel to the liquid and back, the distance, and therefore the level, is calculated.
Radar sensors are highly accurate and can work in extreme conditions, making them suitable for the chemical industry, large industrial tanks, and marine applications. Their adaptability allows for usage with various liquids, even in challenging environments.
Advantages:
- Highly Accurate: Offers very precise readings.
- Extreme Conditions: Functions well in tough environments.
- Versatile: Suitable for various liquids.
Disadvantages:
- Complex Setup: May require professional installation.
- More Expensive: Higher upfront cost.
- Alignment Needed: Proper positioning is crucial.
Magnetostrictive Level Sensor Probes
Magnetostrictive Level Sensor Probes operate by detecting changes in the magnetic alignment within a sensing element. A current pulse generates a magnetic field, interacting with a magnetic float, causing a torsional strain wave. The time taken for this wave to travel is measured, determining the liquid level.
Known for high precision and robust design, these sensors are typically used in petrochemical industries, pharmaceutical manufacturing, and cryogenic applications. Their ability to function in hazardous environments adds to their appeal in these specialized areas.
Advantages:
- High Precision: Extremely accurate readings.
- Robust Design: Suitable for hazardous environments.
- Reliable: Functions well in various industrial settings.
- Large range cable probes can be customized.
Disadvantages:
- More Expensive: Higher cost may limit applications.
- Magnetic Interference: Susceptible to external magnetic fields.
Hydrostatic Level Sensor Probes
Hydrostatic Level Sensor Probes work by measuring the pressure exerted by the liquid at a specific depth, which corresponds to the liquid’s level. The weight of the liquid creates pressure, which the sensor translates into a level reading.
These probes are often utilized in water treatment facilities, sewage systems, deep wells, and fuel tanks.
Their straightforward principle and reliability make them suitable for environments where liquid density is consistent, and there might be slurry or muddy substances, as they can handle such conditions effectively.
Advantages:
- Simple and Reliable: Easy to use and offers dependable readings.
- Works with Muddy Liquids: Suitable for slurry or muddy substances.
- Low Maintenance: Requires minimal upkeep.
Disadvantages:
- Pressure-Sensitive: Changes in pressure may affect performance.
- Regular Cleaning Needed: Thick media may require consistent cleaning.
How to Select the Right Liquid Level Sensor Probe
Selecting the right Liquid Level Sensor Probe is essential for accurate and reliable measurements. Here’s a simple guide to help you choose the best option for your needs:
Understanding Your Needs:
- Liquid Type: Identify if the liquid is conductive, non-conductive, sticky, or corrosive.
- Measuring Range: Determine the maximum and minimum levels that need to be monitored.
- Environmental Conditions: Consider factors like temperature, pressure, humidity, etc., that may affect the sensor.
Evaluating Different Types:
- Material Requirements: Choose materials that are compatible with the liquid being measured, considering factors like corrosion resistance.
- Installation Size: Check the dimensions of the sensor to make sure it fits within the available space.
- Installation Space: Consider the physical layout of the area where the sensor will be installed.
- Signal Output and Signal Control: Determine the type of output needed (analog, digital) and if any specific control features are required, like alarms.
Consideration for Installation and Maintenance:
- Ease of Installation: Look for sensors that can be installed without specialized tools or expertise.
- Maintenance Needs: Understand the cleaning and servicing needs, as some sensors might require more regular maintenance.
By taking these factors into consideration, you can find a Liquid Level Sensor Probe that meets your specific requirements and provides consistent, accurate performance. Remember to consult with experts or refer to detailed product specifications for the best results.
Client Case: Measuring Sulfuric Acid Tanks
We were approached by a customer looking to measure the liquid level in open concrete tanks containing bath acid sulfuric acid. The specific parameters provided were:
- Measured Medium: Bath acid sulfuric acid
- Tank Measurement Range: 2 meters
- Temperature and Pressure: Ambient; maximum atmospheric temperature 30°C
- Mounting Dimensions: 1 1/2″ NPT
After understanding the requirements, we configured the following solution for accurate and reliable measurements:
Radar Level Meters – 80G:
- Application: Measuring the liquid level in sulfuric acid tanks
- Antenna Material: PTFE, for excellent resistance to acid
- Temperature Resistance: -40 to 80℃, suitable for ambient conditions
- Pressure: -0.1 to 0.3MPa, aligning with atmospheric pressure
- Mounting Dimensions: 1 1/2″ NPT PTFE Coated, matching customer’s specifications
- Display: Digital, with measurement and programming capabilities
- Power Supply: 24VDC
- Output: 4-20mA (two wires) + HART
- Electrical Connection: 1/2″ NPT head
This configuration met the customer’s specific needs for measuring sulfuric acid, providing a solution that is both reliable and tailored to their application. The client was satisfied with the performance, praising the gauge’s accuracy and ease of use.
FAQ
More Liquid level measurement Guides
What Is the Ultrasonic CO2 Level Indicator? CO2 Bottle Level Measuring Device
Radar Level Gauge – Everything You Should Know and Selection List
Innovative Methods for Fluid Level Measurement
Grain Bin Level Indicators: The Missing Piece in Your Grain Storage Solution
Radar Antenna Types for Radar Level Meters: How to Choose?
Submersible Pressure Transducers 101: Guide to Precise Level Measurements
Selecting the right Liquid Level Sensor Probe is a critical task, and the various types mentioned offer unique advantages and considerations. Understanding your specific needs and working with an experienced manufacturer can ensure the best solution for your application.
At Sino-Inst, we pride ourselves on being not only an experienced manufacturer but a knowledgeable supplier as well. With years of expertise in the field, we provide tailored solutions to meet your unique needs, even offering customization to align perfectly with your requirements.
If you’re in need of a Liquid Level Sensor Probe, don’t hesitate to reach out to us. Our team is here to assist you in selecting the right product, ensuring efficiency, reliability, and satisfaction. Contact us today and let us be your trusted partner in your liquid level measurement needs.
Request a Quote
Wu Peng, born in 1980, is a highly respected and accomplished male engineer with extensive experience in the field of automation. With over 20 years of industry experience, Wu has made significant contributions to both academia and engineering projects.
Throughout his career, Wu Peng has participated in numerous national and international engineering projects. Some of his most notable projects include the development of an intelligent control system for oil refineries, the design of a cutting-edge distributed control system for petrochemical plants, and the optimization of control algorithms for natural gas pipelines.