MEMS pressure sensors are pressure sensors manufactured using MEMS technology. MEMS pressure sensors include silicon piezoresistive pressure sensors and silicon capacitive pressure sensors.
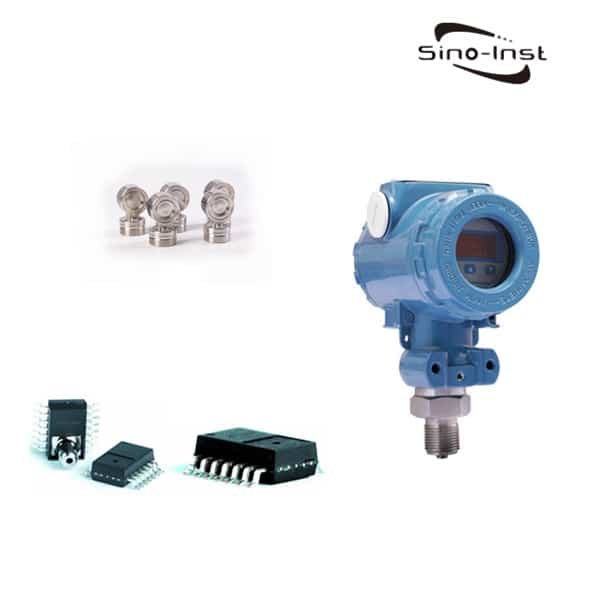
MEMS pressure sensors are the earliest developed miniature sensors with a large market share. MEMS pressure sensors can be divided into piezoresistive and capacitive types. Both are micromechanical electronic sensors generated on silicon chips. MEMS pressure sensors can use high-precision, low-cost mass production with integrated circuit-like design techniques and manufacturing processes. This makes pressure control simple, easy to use, and intelligent. Compared with traditional mechanical quantity sensors, the size of MEMS pressure sensors is smaller, and the largest is no more than one centimeter. Compared with traditional “mechanical” manufacturing technology, its cost performance is greatly improved.
Sino-Inst offers a variety of MEMS pressure senors for industrial pressure measurement. If you have any questions, please contact our sales engineers.
Featured MEMS Pressure Sensors
Features of MEMS Pressure Sensors
- Single crystal silicon sensor using German MEMS technology
- Integrated sensor design using patented technology
- Two-wire system. 4 ~ 20mA analog output. HART® digital communication or four-wire system. RS485 output (MODBUS protocol)
Read more about: What is a pressure sensor and how it works?
Specifications of MEMS Pressure Sensors
Range | Minimum range | DP | Range and sensor limit (kPa) | Minimum range | GP | Range and sensor limit (kPa) | Minimum range | AP | Range and sensor limit (kPa) |
Code | (kPa) | Upper range (URL) | Lower limit of range (URL) | (kPa) | Upper range (URL) | Lower limit of range (URL) | (kPa) | Upper range (URL) | Lower limit of range (URL) |
1 | 0.1 | 1 | -1 | / | / | / | / | / | / |
2 | 0.2 | 5 | -5 | / | / | / | / | / | / |
3 | 0.2 | 20 | -20 | 0.2 | 20 | -20 | / | / | / |
4 | 0.5 | 50 | -50 | 0.5 | 50 | -50 | 0.5 | 50 | 0 |
5 | 2 | 200 | -200 | 2 | 200 | -100 | 2 | 200 | 0 |
6 | 5 | 500 | -500 | 5 | 500 | -100 | / | / | / |
7 | 20 | 2000 | -500 | 20 | 2000 | -100 | 20 | 2000 | 0 |
8 | 100 | 10000 | -500 | 100 | 10000 | -100 | 100 | 10000 | 0 |
9 | / | / | / | 400 | 40000 | -100 | / | / | / |
- Sensor type: German MEMS technology single crystal silicon sensor
- Range ratio: 100: 01: 00
- Accuracy grade: 0.075, 0.1, 0.2
- Stability: 36 months error is ± 0.2% of maximum range
- Temperature effect:
- “0.075 level: zero point or range error is ± 0.15% / 28 ℃ of maximum range
- 0.1 level: Zero point or range error is ± 0.2% / 28 ℃ of maximum range
- Level 0.2: Zero point or range error is ± 0.25% of maximum range / 28 ℃ “
- Output signal: “Two-wire system, 4 ~ 20mA DC, HAR T® protocol digital signal. Or four-wire system, RS485 output (MODBU S protocol)”
- Metrology certification: CMC
- Explosion-proof certification: “Explosion-proof type: Exd IIC T6 Gb
Intrinsically safe type: Exia IIC T6 Ga or Exib IIC T4 Gb “ - Protection grade: IP67
You may like: Explosion Proof Pressure Transmitter for Hazardous locations
What does MEMS mean?
MEMS is the abbreviation of Micro-Electro-Mechanical Systems. MEMS is the name of the United States. In Japan, it is called micromachine. In Europe, it is called microsystem. MEMS refers to mass production, which integrates micro-mechanisms, micro-sensors, micro-actuators, signal processing and control circuits, and interfaces. , Communication and power supply are equal to a micro device or system. MEMS is developed with the development of 1653 technology for semiconductor integrated circuit micromachining and internal ultra-precision mechanical processing technology. Currently MEMS processing technology is also widely used in microfluidic chips and synthetic biology. Chip integration of the technical process of the actual volume laboratory.
What is a MEMS pressure sensor?
MEMS pressure sensor is a pressure sensor manufactured by MEMS technology.
MEMS pressure sensors are the earliest developed miniature sensors with a large market share. The current application field has been greatly expanded, far beyond the traditional applications in industrial transmitters and other fields. Generally, MEMS pressure sensors are made by bulk silicon processing technology, and some are made by surface silicon processing technology. MEMS pressure sensors can be divided into piezoresistive and capacitive. Similar to other sensors, the MEMS pressure sensor converts the pressure into an electrical signal output during operation.
Extended Reading: Digital Pressure Sensor-RS485
Piezoresistive MEMS pressure sensor
The piezoresistive MEMS pressure sensor uses a high-precision semiconductor resistance strain gauge to form a Wheatstone bridge as a force-electric conversion measurement circuit. It has high measurement accuracy, low power consumption, and extremely low cost.
Capacitive MEMS pressure sensor
Capacitive pressure sensors use MEMS technology to produce a diaphragm grid on the silicon wafer. The upper and lower diaphragms become a group of capacitive pressure sensors. The upper diaphragm is displaced downward by pressure and changes the upper and lower diaphragms. The spacing of the grids also changes the capacitance between the plates, that is, △ pressure = △ capacitance
Read more about: Capacitive pressure transducer
How does a MEMS pressure sensor work?
The MEMS piezoresistive pressure sensor uses a circular stress cup silicon film inner wall fixed around the periphery. MEMS technology is used to directly engrave four high-precision semiconductor strain gauges on the surface with the highest stress. Make up the Wheatstone measuring bridge. As a force-electricity conversion measurement circuit. The physical quantity of pressure is directly converted into electricity. The measurement accuracy can reach 0.01% ~ 0.03% FS.
You may like: How does a pressure transmitter work?
The MEMS capacitive pressure sensor uses MEMS technology to produce a diaphragm grid on the silicon chip. The two upper and lower diaphragms become a group of capacitive pressure sensors. The upper MEMS capacitive pressure sensors use MEMS technology to create a grid-like shape on a silicon wafer. The two upper and lower transverse barriers become a group of capacitive pressure sensors. The upper diaphragm is displaced downward by pressure. Changed the spacing between the upper and lower two horizontal barriers. It also changes the size of the capacitance between the boards.
Video on How MEMS Pressure Sensor Operation:
Video source: https://www.youtube.com/watch?v=juf4d3sgOJw
Applications of MEMS Pressure Sensors
- Applied in the automotive industry
A new application of MEMS pressure sensors in automobiles is the transmission system pressure sensing. It is usually used in automatic devices. But it is also used in new dual clutch transmission systems. German manufacturers have introduced a MEMS solution that uses oil to protect the silicon film so that it can withstand pressures up to 70 bar. Bosch also brought huge changes to MEMS pressure sensors a few years ago. At that time, porous silicon was used to bring highly reliable MEMS devices. These devices have been used in current side airbag applications. - Applied to the medical market
The pressure sensor mainly serves as a disposable low-cost catheter for surgical operations. But they are also used in expensive equipment. Sensing pressure and differential flow in continuous positive airway pressure (CPAC) machines. - Applied in the industrial field
The main applications of MEMS pressure sensors include heating, ventilation and air conditioning (HVAC), water level measurement, and various industrial process and control applications. For example, in addition to accurate altitude and barometric pressure measurements, aircraft use sensors to monitor engines, flaps, and other components.
Extended reading: What is a pressure sensor?
Frequently
Asked
Questions
More Pressure Measurement Solutions
Sino-Inst offers over 20 MEMS Pressure Sensors. About 50% of these are 4-20ma Low-Pressure Transducers, 40% are Differential Pressure Gauge, and 20% are Diaphragm Seal Pressure transmitters, 20% are 4-20ma differential pressure transmitters.
A wide variety of MEMS Pressure Sensors options are available to you, such as free samples, paid samples. Sino-Inst is a globally recognized supplier and manufacturer of Pressure Transducers, located in China.
You can ensure product safety by selecting from certified suppliers, with ISO9001, ISO14001 certification.
Request a Quote
Wu Peng, born in 1980, is a highly respected and accomplished male engineer with extensive experience in the field of automation. With over 20 years of industry experience, Wu has made significant contributions to both academia and engineering projects.
Throughout his career, Wu Peng has participated in numerous national and international engineering projects. Some of his most notable projects include the development of an intelligent control system for oil refineries, the design of a cutting-edge distributed control system for petrochemical plants, and the optimization of control algorithms for natural gas pipelines.