Industrial pressure transmitters for the process pressure measure, monitor and control application.
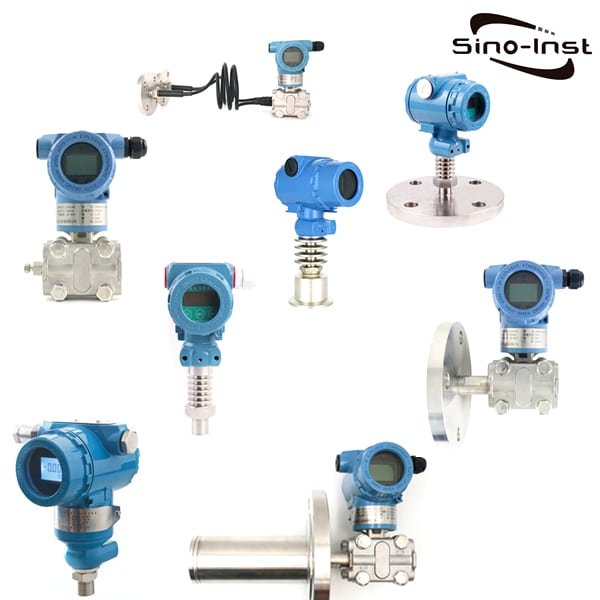
Industrial pressure transmitters are sensors with electrical transmission output for remote indication of pressure. Process transmitters differentiate themselves from pressure sensors through their increased range of functionality.
They feature integrated displays, offer high measuring accuracies and freely scalable measuring ranges. Communication is via digital signals, and waterproof and explosion-proof certifications are available. Through connection to diaphragm seals, they are suitable for the harshest operating conditions. Ideal for OEMs, process applications, water processing, and industrial pressure applications.
Sino-Inst offers a variety of pressure senors for industrial pressure measurement. If you have any questions, please contact our sales engineers.
Featured Industrial Pressure Transmitters
A gauge pressure (GP) transmitter compares a process pressure against local ambient air pressure. Gauge pressure transmitters have ports to sample the ambient air pressure in real-time.
Gauge pressure (GP) transmitters compare process pressure with local ambient air pressure. Gauge pressure transmitters have ports for real-time sampling of ambient air pressure.
Explosion-proof Pressure transmitter, or explosion-proof pressure transducer, with the explosion-proof enclosure.
For applications in hazardous areas.
When the process medium should not come into contact with the pressured parts of the measuring instrument. Diaphragm sealed pressure transmitters are used for pressure measurement.
Also called Hygienic pressure Transmitters, or tri clamp pressure transmitter. Sanitary pressure Transmitters is used to food &beverage or pharmaceutical application.
High-temperature pressure transmitters with a 4-20mA output.
which has a temperature capability of over 850 °C and is not pyroelectric.
Absolute pressure transmitter with 4-20mA output for measuring pressure with absolute type reference. Absolute pressure (AP) transmitter is a measure of the ideal (complete) vacuum pressure.
Hydrostatic pressure transmitter is used for fluid hydrostatic pressure measurement. With working static pressure up to 32Mpa, for liquid, gas or steam .
Remote seal pressure transmitter, with capillary and diaphragm seal, remote mount. Diaphragm seal systems protect pressure transmitters from hot, viscous, contaminated or corrosive media.
Sino-Inst also provides repair services for Industrial pressure transmitters. Such as WIKA, Rosemount, and other brands of pressure transmitters.
What is a smart pressure transmitter?
Digital smart pressure transmitter is pressure sensor with a 12-bit or higher microprocessor. Smart pressure transmitters are high performance microprocessor-based transmitters with flexibility. Pressure calibration and output, automatic compensation.
Smart pressure transmitter also called intelligent pressure transmitter.
The intelligent Industrial pressure transmitters consist of two parts: a smart sensor and a smart electronic board.
The smart sensor part includes: a capacitive sensor. A measuring diaphragm detection circuit. A temperature sensor, and a temperature compensation circuit.
The smart electronic board includes: a microcomputer controller. And the peripheral circuit, complete the pressure signal to 4 ~ 20mA dc conversion.
Smart Industrial pressure transmitter is used to measure the pressure of liquid, gas or steam. And then convert the pressure signal into 4 ~ 20mA DC signal output. The intelligent pressure transmitter produced by Sino-Inst can communicate with the HART communicator. It is widely used in weakly corrosive liquids in industrial pipelines, Gas and steam measurement and control systems.
Industrial pressure transmitters Working Principle
Principle and Application of Diffusion Silicon Pressure Transmitter
The pressure of the measured medium directly acts on the diaphragm of the sensor (stainless steel or ceramic). Causing the diaphragm to generate a micro-displacement proportional to the pressure of the medium. The resistance value of the sensor changes. The electronic circuit detects this change and converts and outputs a standard measurement signal corresponding to this pressure.
Principle of capacitive pressure transmitter
Capacitive pressure transmitter is mainly composed of capacitance sensor and circuit board. The sensor implements pressure-capacitance conversion. The circuit board converts the capacitance to a two-wire 4-20mA.
When the process pressure is applied to the isolation diaphragm from both sides (or one side) of the measuring chamber, it is transferred to the central diaphragm of the chamber through the silicone oil filling liquid. The central diaphragm is a diaphragm with tensioned edges.
Under the action of pressure, a corresponding displacement is generated. This displacement creates a change in differential capacitance!
And through the adjustment, oscillation and amplification of the electronic circuit board! Converted into 4-20mA signal output! The output current is directly proportional to the process pressure!
Types of Pressure Transmitters
Depending on the type of pressure to be measured:
Pressure transmitter types include gauge pressure, absolute pressure, and differential pressure. Gauge pressure refers to the pressure that is less than or greater than atmospheric pressure based on the atmosphere. Absolute pressure refers to the absolute zero pressure as the reference and is higher than the absolute pressure. Differential pressure refers to the difference between two pressures.
According to the working principle of the Industrial pressure transmitters:
- Strain Gauge Pressure Transducers
- Capacitance Pressure Transducers
- Potentiometric Pressure Transducers
- Resonant Wire Pressure Transducers
Electrical Output of Pressure Transducers
Pressure transmitters are generally available with three types of electrical output. Millivolt, amplified voltage and 4-20mA. Below is a summary of the outputs and when they are best used.
Extended Reading: 4-20ma pressure transducer wiring diagram
Millivolt Output Pressure Transducers
A sensor with a millivolt output is usually the most economical pressure sensor. The output of a millivolt sensor is nominally about 30mV. The actual output is proportional to the input power or excitation of the pressure sensor. If the stimulus fluctuates, the output will change.
Because of this dependence on the level of excitation, a regulated power supply is recommended for millivolt sensors. Because the output signal is so low, the transducer should not be placed in an electrically noisy environment. The distance between the transducer and the reading instrument should also be kept relatively short.
Voltage Output Pressure Transducers
Voltage output transducers include integral signal conditioning, which provides higher output than millivolt transducers. The output is usually 0-5Vdc or 0-10Vdc. Although model-specific, the output of the transducer is usually not a direct function of the stimulus. This means that as long as the regulated power supply falls within the specified power range, it is usually sufficient. Because of their higher output levels, these sensors are not as susceptible to electrical noise as millivolt sensors and can therefore be used in more industrial environments.
4-20 mA Output Pressure Transducers
These types of sensors are also called pressure transmitters. Because 4-20mA signals are least affected by electrical noise and resistance in the signal line, these sensors are best used when signals must be transmitted over long distances. These sensors are typically used in applications where the lead must be 1000 feet or more.
Industrial Applications of Pressure Transmitters
Pressure transmitters are mainly used in the following areas:
- Petroleum, petrochemical, chemical. Matching with throttling devices to provide accurate flow measurement and control. Measures pressure and level in pipes and tanks.
- Electricity, city gas. And other companies and businesses require high stability and high precision measurement and other places.
- Pulp and papermaking are used in places that require chemical-resistant liquids and corrosion-resistant liquids.
- Steel, non-ferrous metals, and ceramics are used in furnace pressure measurement and other places that require high stability and high precision measurement. They are also used in places that require stable measurement under strict control (temperature, humidity, etc.).
- Machinery and shipbuilding, used to strictly control the place where high precision is required for stable measurement.
Hydrostatic pressure for level measurement:
Pressure Transmitters VS Pressure Sensors VS Pressure Transducers
A pressure sensor is a device or device that can sense a pressure signal and convert the pressure signal into a usable output electrical signal according to a certain rule.
A pressure sensor usually consists of a pressure-sensitive element and a signal processing unit. According to different test pressure types, pressure sensors can be divided into gauge pressure sensors, differential pressure sensors and absolute pressure sensors. A pressure sensor is the core part of pressure transmitter.
In a pressure transducer, a thin-film or piezo-resistive pressure sensor is mounted on a process connection. The transducer converts pressure into an analog electronic output signal, typically as a millivolt per volt output. These signals are not linearized or temperature compensated.
A pressure transmitter has additional circuitry that linearizes, compensates, and amplifies the signal from a transducer. The different signal types are typically voltage signals (eg, 0 to 5 or 0 to 10 volts), milliamp (eg, 4 to 20 milliamp), or digital. The instrument then can transmit the signal to a remote receiver.
If you still don’t know how to choose the right pressure transmitter. Please feel free to contact our sales engineers. We will provide you with the best pressure measurement and control solution.
Guidelines for Troubleshooting Pressure Transmitters
When this happens, you should consider: Is the pressure source itself stable? The degree of anti-interference ability of the instrument or pressure sensor. Is the sensor wiring normal? The sensor itself is vibrating and the cause of the failure. Is the polarity of the power supply reversed?
Check the degree of pressure variable; make 4-20mA output adjustment.
Check the transmitter’s power supply voltage, calibration equipment and set values (4mA and 20mA points). Check whether the pressure interface is leaking or blocked. Check the wiring mode and power supply. If normal, check if the sensor has zero output. Or Perform a simple pressurization to see if the output changes. If there is a change, the sensor is not damaged.
Check if pressure transmission is blocked; check calibration equipment and adjust sensors; check vehicle damping and electromotive force interference.
Frequently
Asked
Questions
Related Products
Related Blogs
Sino-Inst offers over 20 industrial pressure transmitters.
A wide variety of industrial pressure transmitters options are available to you. Such as free samples, paid samples.
Sino-Inst is a globally recognized manufacturer of industrial pressure transmitters, located in China.
Sino-Inst sells through a mature distribution network that reaches all 30 countries worldwide.
Industrial pressure transmitters products are most popular in Europe, Southeast Asia, and Mid East. You can ensure product safety by selecting from certified suppliers. With ISO9001, ISO14001 certification.
Request a Quote
Wu Peng, born in 1980, is a highly respected and accomplished male engineer with extensive experience in the field of automation. With over 20 years of industry experience, Wu has made significant contributions to both academia and engineering projects.
Throughout his career, Wu Peng has participated in numerous national and international engineering projects. Some of his most notable projects include the development of an intelligent control system for oil refineries, the design of a cutting-edge distributed control system for petrochemical plants, and the optimization of control algorithms for natural gas pipelines.