High pressure sensor is pressure transmitter designed for high pressure measure&control. 0 ~ 40MPa… 600MPa.
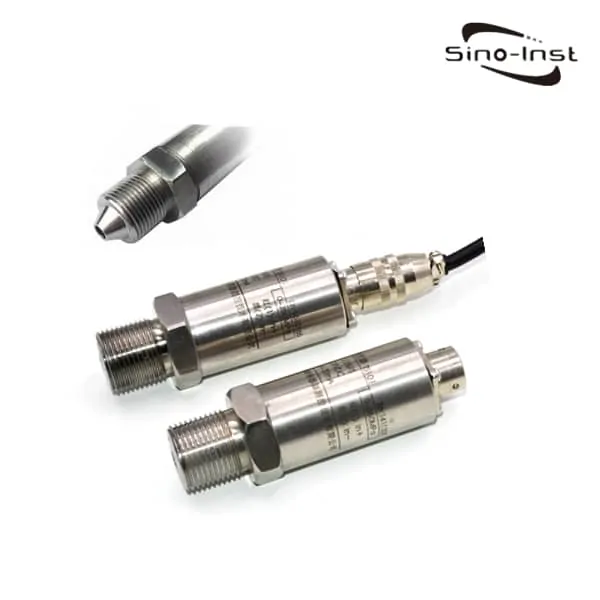
High pressure sensor elastic body adopts special material and integrated structure design. SI-702 high pressure sensor has no burst phenomenon during high voltage measurement and control. The high pressure sensor is used under high pressure, differential high pressure and high pressure shock conditions. High pressure sensors are suitable for pressure measurement & control of large hydraulic equipment. SI-702 high pressure sensor adopts spherical or cone seal to ensure the tightness of high voltage system. Such sensor also referred to as: high pressure pressure sensor, high pressure transmitter.
Sino-Inst offers a variety of High Pressure sensors for industrial pressure measurement. If you have any questions, please contact our sales engineers.
More High Pressure Sensors:
Features of SI-702 High Pressure Sensor
- Adopt resistance strain gauge pressure sensor chip. The selected patch technology has zero point, full scale compensation and temperature compensation;
- High precision and high stability amplifier integrated circuit;
- Micro-mechanical processing technology, integrated structure of measuring diaphragm and pressure interface. Impact resistance, fatigue resistance, high reliability;
- Integrated design product will not rupture under pressure of 1100MPA, ensuring product safety
- Diversified output signals (general-purpose analog output, digital RS485 / RS232 output, GPRS wireless transmission);
- Small structure, minimum outer diameter can reach 26mm. Can be directly matched with local display meter (output is 4-20mA two-wire system);
- Thread interface adopts 7 degree cone sealing surface;
Specifications of SI-702 High Pressure Sensor
Pressure type | Gauge/ Absolute | Pressure range | 0-80,100,150,200,250,300MPa, …600MPa. |
Precision | ±0.1%FS ±0.3%FS ±0.5%FS | Zero temperature drift | ±0.02%FS/℃ |
Sensitivity temperature drift | ±0.02%FS/℃ | Long-term stability (1 year) | ±0.1%FS |
Response frequency (-3dB) | 3.2KHz | Temperature compensation | -20~+85℃ |
Operating temperature | -40~+125℃ | Storage temperature | -40~+125℃ |
Overload pressure | 150%FS | Destruction pressure | 300% FS (limit pressure 10000bar) |
Protection class | IP65 | Material | 17-4PH |
Electrical connections | Direct lead, M12 connector, Big Hessman, Little Hessman | Pressure connection | M20 × 1.5, G1 / 2 (others are customized according to requirements) |
Signal output | 4~20mA | 0.5~4.5VDC (Proportional output) | 0.5~4.5VDC | 0~5VDC | 0-10VDC |
Signal cable specifications | 2 Wire | 3 Wire | 3 Wire | 3 Wire | 3 Wire |
Supply voltage | 9~30VDC | 5VDC | 9~30VDC | 9~30VDC | 15~30VDC |
Extended reading: High Pressure Flow Meters for Liquids-Steam-Gas
Applications of SI-702 High Pressure Sensor
- Pressure measurement of large hydraulic machinery and hydraulic stations;
- Pressure measurement and control of water jet cutter and ceramic wire cutter;
- Pressure measurement of high pressure water pump and high pressure oil pump;
- Supporting heavy equipment
- high pressure
- High load
- High impact
- Frequently overloaded areas
Extended Reading: Digital Pressure Sensor-RS485
Dimensions of High pressure sensors
What is High Pressure Sensor?
High pressure transducer is a pressure transmitter suitable for high pressure measurement and co
A high pressure sensor is a device for high pressure measurement of gases or liquids. A high pressure sensor usually acts as a transducer; it generates a signal as a function of the pressure imposed. Such a signal is electrical 4-20mA, 0-5V,etc.
High Pressure sensors are used for control and monitoring in thousands of everyday applications. High Pressure sensors can also be used to indirectly measure other variables such as fluid/gas flow, speed, water level, and altitude. High Pressure sensors can alternatively be called High pressure transducers, High pressure transmitters, High pressure senders, High pressure indicators, piezometers and manometers, among other names.
Sino-Inst high pressure sensor has gone through thousands of fatigue impact tests and several days of low and medium temperature aging cycles before leaving the factory. It has solved the disadvantages of high pressure sensors in terms of stress and zero instability. Provide customers with reliable products for high voltage measurement. The pressure of SI-702 series can reach 600MPa. The precision level is high, and the mature production technology can ensure the long-term stability of the sensor with excellent characteristics. SI-702 series pressure sensors are suitable for oil extraction platforms, water flow equipment, high pressure measurement equipment, hydraulic control systems, test benches and industrial automation control.
You may like: How does a pressure transmitter work?
Technical Support
High Temperature Pressure Sensor
High Temperature Pressure Sensor with high temperature resistant pressure core or sapphire core as pressure measurement material. After high reliability amplifier circuit and precise temperature compensation. The absolute or gauge pressure of the measured medium is converted into standard electrical signals such as 4 ~ 20mA, 0 ~ 5VDC, 0 ~ 10VDC. It is also widely used in industry. Collect pressure signals at the points of some high-temperature steam and fluid pipes.
How do you use a pressure sensor?
1. The key points in the use of pressure sensors and the correct installation position of the transmitter on the process pipeline are related to the measured medium. Only by mastering the correct use of the pressure sensor can the best measurement results be obtained!
2. Prevent the transmitter from coming into contact with corrosive or hot media.
3. Prevent dross from depositing in the duct.
4. When measuring liquid pressure, the pressure taking port should be opened on the side of the process pipeline to avoid sedimentation.
5. When measuring the gas pressure, the pressure taking port should be opened at the top of the process pipeline. The transmitter should also be installed at the top of the process pipeline so that the accumulated liquid can be easily injected into the process pipeline.
6. The pressure guiding tube should be installed in a place with small temperature fluctuations.
7. When measuring steam or other high-temperature media, a condenser such as a buffer tube (coil) must be connected. The transmitter’s operating temperature should not exceed the limit.
Q&A
What is pressure sensor and how it works?
A pressure sensor is a device for pressure measurement of gases or liquids. Pressure sensors can also be used to indirectly measure other variables such as fluid/gas flow, speed, water level, and altitude. Pressure sensors can alternatively be called pressure transducers, pressure transmitters, pressure senders, pressure indicators, piezometers, and manometers, among other names.
In short, a pressure sensor converts pressure into a small electrical signal, which is sent and displayed. Therefore, these are also commonly referred to as pressure transmitters. Two common signals used are 4 to 20 mA signals and 0 to 5-volt signals.
Most pressure sensors work using the piezoelectric effect. This is when the material generates a charge in response to stress. This stress is usually compressive, but may be twisted, bent, or vibrated.
Pressure sensors detect pressure and can determine the amount of pressure by measuring the charge.
The pressure sensor needs to be calibrated in order to know what voltage or milliamp (mA) signal corresponds to what pressure. This is the basic “zero” and “span” calibration or minimum and maximum, which is a common job for maintenance personnel.
Read more about: What is a pressure sensor and how it works?
What does a barometric pressure sensor do?
Air pressure sensor is an instrument used to measure the absolute pressure of gas. Air pressure sensor is mainly suitable for physical experiments related to gas pressure. It can also measure dry, non-corrosive gas pressure in biological and chemical experiments.
The main sensing element of the air pressure sensor of the air compressor is a thin film that is sensitive to the pressure of the air pressure and a thimble opening control. In the circuit, it is connected with a flexible resistor. When the pressure of the measured gas decreases or increases, the thin film deforms to drive the ejector pin, and the resistance of the resistor will change. The resistance of the resistor changes. The signal voltage of 0-5V is obtained from the sensing element, and is received by the data collector after A / D conversion, and then the data collector transmits the result to the computer in an appropriate form.
The main component of many air pressure sensors is a variable-capacitance silicon capsule. When the external atmospheric pressure of the variable-capacitance silicon membrane box changes, the thimble moves, and the single crystal silicon membrane box elastically deforms with it, thereby causing a change in the capacitance of the parallel plate capacitor of the silicon membrane box to control the air pressure sensor.
More about Gas Pressure Sensor.
What are pressure sensors made of?
The pressure sensor is a device that detects pressure and converts the pressure signal into an electrical signal and outputs it linearly. Common types include strain gauge, piezoresistive, capacitive, piezoelectric, and vibration frequency pressure sensors.
We use strain gauge pressure sensors as an introduction. It is mainly composed of 4 parts: elastomer, strain gauge, measuring circuit and transmission cable.
Strain gauge pressure sensor measurement principle: When the pressure sensor elastic body is deformed under the action of external force. The strain gauge attached to the elastic body then bends. The resistance of the strain gauge changes. Then the measurement circuit converts the change in resistance into an electrical signal (usually a millivolt signal).
Elastomer: Elastomer is the pressure sensor shell. The main materials are aluminum alloy, alloy steel and stainless steel.
Strain gauge: The strain gauge pressure is an important part of the sensor. Commonly used strain gauge base material adopts polymer film material. The strained material is usually high-purity constantan. The strain gauge is attached to the elastic body through dehydration. The elastic body is deformed by force. The strain gauge then deforms. Thereby changing the resistance value.
Measurement circuit: Transform the resistance change of the strain gauge into a millivolt signal output through the Wheatstone bridge.
Transmission cable: 4-core shielded cable with four wires of red, black, green and white. Red: Power +. Black: Power-. Green: signal +. White: Signal-.
What is the difference between pressure switch and pressure sensor?
Pressure Switch:
As the name suggests, a pressure switch is a switch. It’s just that this switch is the pressure set in advance. When the measured medium reaches this pressure level, the switch can automatically turn on or off. The pressure switch must be given a pressure value in advance. Then turn the switch on or off. They are used for simple control and are all digital outputs.
Pressure Sensor:
The pressure sensor can output not only analog signals but also digital signals. Digital signal processing is more convenient, and remote transmission is also possible. The pressure sensor is composed of a pressure sensitive element and a conversion circuit. Use the pressure of the measured medium to produce a small change in current or voltage output on the pressure sensitive element.
Sino-Inst offers High pressure sensors. A wide variety of High Pressure sensors options are available to you. Such as free samples, paid samples. Sino-Instrument is a globally recognized manufacturer of High Pressure sensors, located in China. Sino-Inst sells through a mature distribution network that reaches all 30 countries worldwide. Pressure sensors products are most popular in Europe, Southeast Asia, and Mid East. You can ensure product safety by selecting from certified suppliers. With ISO9001, ISO14001 certification.
Request a Quote
Wu Peng, born in 1980, is a highly respected and accomplished male engineer with extensive experience in the field of automation. With over 20 years of industry experience, Wu has made significant contributions to both academia and engineering projects.
Throughout his career, Wu Peng has participated in numerous national and international engineering projects. Some of his most notable projects include the development of an intelligent control system for oil refineries, the design of a cutting-edge distributed control system for petrochemical plants, and the optimization of control algorithms for natural gas pipelines.