Turbine Flow Meter Installation Guidelines and Troubleshooting is compiled based on our Sino-Inst’s many years of experience in producing and supplying turbine flow meters.
Whether it is a liquid turbine flow meter or a gas turbine flow meter. In order to ensure that the measurement of the turbine flowmeter is accurate. The installation location and installation precautions must be correctly selected.
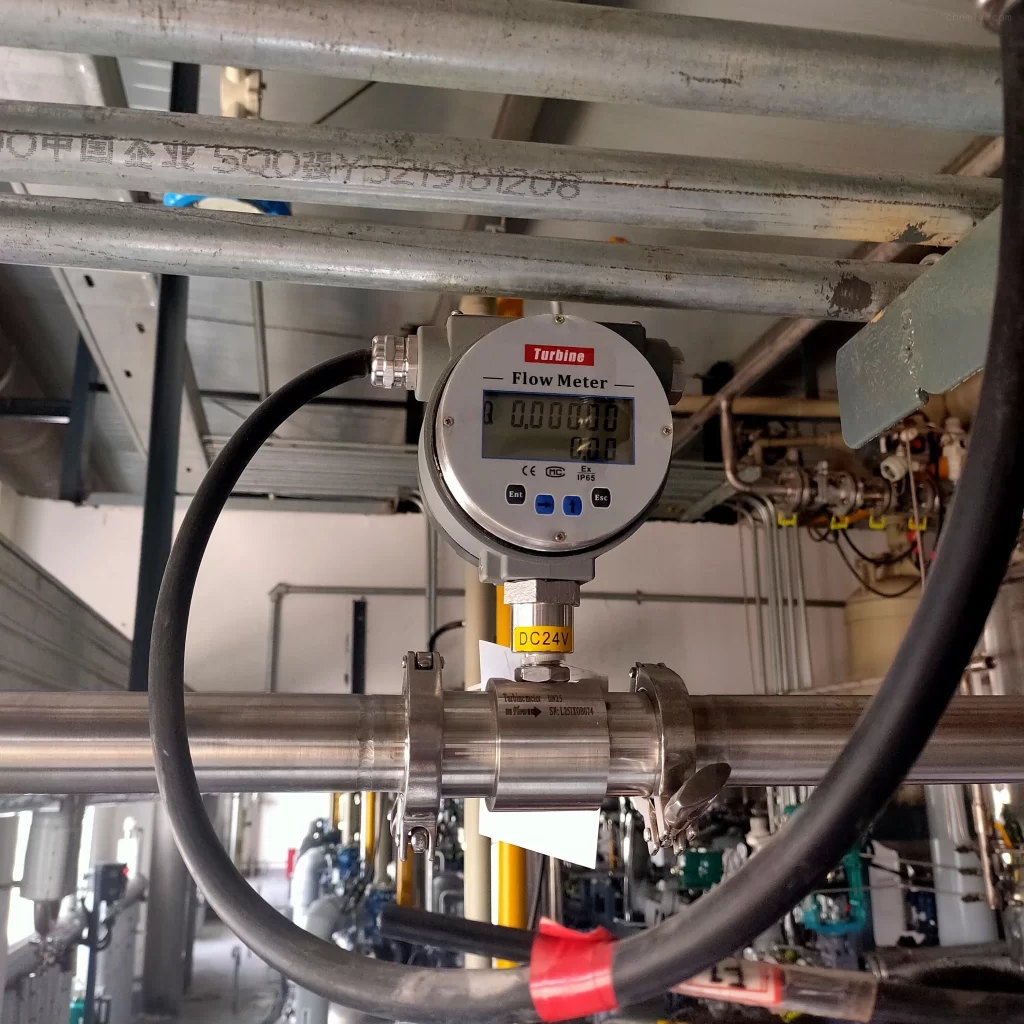
Liquid Turbine Flow Meter Installation Guidelines
Installation Location
The sensor should be installed in a place that is easy to maintain, has no vibration in the pipeline, and is not affected by strong electromagnetic interference and heat radiation.
A typical installation piping system for a turbine flowmeter is shown in the figure.
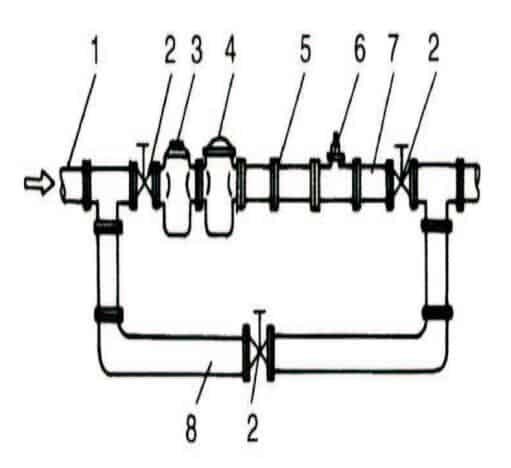
1 – entrance;
2-valve;
3 – filter;
4 – air eliminator;
5- front straight pipe section;
6 – sensor;
7- rear straight pipe section;
8-Bypass
The configuration of each part in the figure depends on the situation of the measured object, not necessarily all of them.
Turbine flowmeters are sensitive to distortion of flow velocity distribution and swirling flow in the pipeline, and the flow into the sensor should be fully developed. Therefore, the necessary straight pipe section or flow regulator should be equipped according to the type of choke on the upstream side of the sensor, as shown in the table below.
If the condition of the upstream side choke is not clear, it is generally recommended that the length of the upstream straight pipe section is not less than 20D, and the length of the downstream straight pipe section is not less than 5D. If the installation space cannot meet the above requirements, a flow regulator can be installed between the choke and the sensor.
When the sensor is installed outdoors, measures should be taken to avoid direct sunlight and rain.
Type of spoiler on the upstream side | Single 90° elbow | Two 90° elbows on the same plane | Two 90° elbows on different planes | Concentric reducer | Fully open valve | Hhalf open valve | Downstream side length |
L/DN | 20 | 25 | 40 | 15 | 20 | 50 | 5 |
Installation Requirements for Connecting Pipelines
The sensor installed horizontally requires that the pipeline should not have a visually detectable inclination (generally within 5°). The verticality deviation of the sensor pipe installed vertically should also be less than 5°. The fluid direction must be upward when installed vertically.
Where continuous operation is required and the flow cannot be stopped, bypass pipes and reliable stop valves should be installed. When measuring, make sure that there is no leakage in the bypass pipe.
In the position where the sensor is installed in the newly laid pipeline, a short pipe is first inserted to replace the sensor. After the “line sweeping” work is completed and the pipeline is cleaned, the sensor is formally connected. Due to neglect of this task, it is not uncommon for wire sweeping to damage the sensor.
If the fluid contains impurities, a filter should be installed on the upstream side of the sensor. For those that cannot stop the flow, two sets of filters should be installed in parallel to remove impurities in turn, or self-cleaning filters should be selected.
If the measured liquid contains gas, a muffler should be installed on the upstream side of the sensor. The sewage outlet and air elimination outlet of the filter and muffler should lead to a safe place.
If the installation position of the sensor is at the low point of the pipeline, in order to prevent the impurities in the fluid from settling and stagnating. A discharge valve should be installed in the subsequent pipeline to discharge the precipitated impurities regularly.
The flow regulating valve should be installed downstream of the sensor, and the stop valve on the upstream side should be fully open when measuring. And these valves must not produce vibration and leak outward. For processes that may generate reverse flow, check valves should be added to prevent reverse flow of fluid.
The sensor should be concentric with the pipe, and the sealing gasket should not protrude into the pipe. Liquid sensors should not be installed at the highest point of the horizontal pipeline. In order to prevent the gas accumulated in the pipeline (such as mixed gas when the flow is stopped) staying at the sensor, it is not easy to discharge and affect the measurement.
The pipelines before and after the sensor should be supported firmly without vibration. For condensable fluids, thermal insulation measures should be taken for the sensor and its front and rear pipelines.
Installation Requirements
- The pipe must be completely filled with liquid. It is important to keep the tubing completely filled with fluid at all times. Otherwise the traffic display will be affected. Measurement errors may result.
- Avoid air bubbles. If air bubbles enter the measuring tube, the flow display may be affected, possibly causing measurement errors.
Straight pipe requirements
- Generally
- 90° elbow
- Two 90° elbows on the same plane
- Two 90° elbows on different planes
- shrink tube
- Expansion
- Fully open valve
- half open valve
- If the condition of the upstream side choke is not clear, it is generally recommended that the length of the upstream straight pipe section is not less than 20D, and the length of the downstream straight pipe section is not less than 5D.
- If the installation control cannot meet the above requirements, a rectifier can be installed between the baffle and the sensor.
Gas Turbine Flow Meter Installation Guidelines
When installing the Gas Turbine Flow Meter, the user must carefully read the following content. Because the condition of the installation of the flowmeter directly affects the accuracy and life of the flowmeter, and even safety issues during work.
- The installation work must be performed by personnel with corresponding pipeline equipment installation skills;
- The flowmeter should be installed in a place that is convenient for maintenance, no strong electromagnetic field interference, no mechanical vibration and thermal radiation influence;
- When the flowmeter is installed outdoors, there should be a cover on the upper part to prevent rainwater and hot sun from affecting the service life of the flowmeter;
- When the flowmeter is installed, it is strictly forbidden to conduct electric welding directly at its inlet flange to avoid burning the internal parts of the flowmeter;
- The newly installed or overhauled pipeline must be cleaned, and the flowmeter can be installed after removing the debris in the pipeline;
- The flowmeter can only be installed horizontally, not vertically. The fluid flow direction should be consistent with the direction marked on the housing. There should be a straight pipe section ≥ 2DN upstream of the flowmeter, and a straight pipe section ≥ 1DN downstream of the flowmeter. Straight pipe section, and the filter of the corresponding specification must be installed at the upstream of the flowmeter (≥2DN) (the company can match) to prevent excessive particulate impurities in the pipeline from entering the flowmeter and affecting the service life of the meter;
- The flowmeter should not be used in occasions where the flow is frequently interrupted and there is a strong pulsating flow or pressure pulsation;
- Ensure that the connection between the pipeline and the inlet and outlet of the flowmeter is coaxial, and prevent gaskets and welds from protruding into the pipeline, otherwise the flow profile will be disturbed;
- In order to facilitate the maintenance of the instrument, it is recommended to install the bypass pipeline according to Figure 6. Open the bypass when the instrument is maintained so as not to affect the normal production, and close the bypass pipeline during normal use.
- When the flowmeter is put into operation, the upstream valve of the flowmeter should be slowly opened, and then the downstream valve of the flowmeter should be slowly opened, so as to avoid the instantaneous air flow that will destroy the turbine flowmeter;
- The flowmeter must be reliably grounded as specified, but must not share the ground wire with the strong current system; during pipeline installation or maintenance, the ground wire of the electric welding system must not be overlapped with the flowmeter;
- During use, users are not allowed to change the connection method of the explosion-proof system and change the lead interface arbitrarily;
Read more about: What are the application of turbine flow meters?
Turbine Flow Meter Installation Troubleshooting
Fault phenomenon | Causes and Solution |
1. There is no display when the liquid flows normally, and the cumulative volume does not increase | 1) The power supply circuit or signal circuit is disconnected or poorly connected. Troubleshooting method: check with a multimeter to eliminate the fault point; 2) The printed circuit board of the display instrument, the connector is faulty or the contact is poor. Remedy: replace the printed circuit board; 3) The preamplifier is faulty. Troubleshooting method: Use an iron bar to move quickly under the detection head, if there is no signal output, check whether the coil is disconnected or the solder joint is desoldered; 4) The voltage supplied to the preamplifier is too low. Troubleshooting method: increase the power supply voltage to the specified requirements; 5) The impeller is stuck and does not rotate. Troubleshooting method: remove foreign matter, and clean or replace damaged parts, and re-calibrate after replacing parts; |
2. When the flow is zero, the flow display is not zero, and the displayed value is unstable | 1) Poor shielding and grounding of the transmission line, interference from the external electromagnetic field. Troubleshooting method: check the grounding and eliminate interference; 2) The pipeline vibrates, causing the impeller to vibrate. Troubleshooting method: strengthen the pipeline or install brackets before and after the flowmeter; 3) The shut-off valve is leaking. Troubleshooting method: overhaul or replace the valve; 4) Interference between circuit boards or electronic components inside the display is deteriorated and damaged. Troubleshooting method: take short circuit method”” or check one by one to find out the fault point;” |
3. The displayed traffic does not match the actual traffic | 1) The impeller is corroded and the blades are deformed. Troubleshooting method: Repair the impeller or re-calibrate after replacement; 2) The sundries hinder the rotation of the impeller. Troubleshooting: Clearing Debris; 3) The output signal of the detection coil is abnormal. Troubleshooting method: check the coil insulation resistance and conduction resistance; 4) The bypass valve is leaking. Troubleshooting method: close the bypass valve and replace it if necessary; 5) The flow velocity distribution upstream of the flowmeter is distorted or pulsating flow occurs. Troubleshooting method: find out the cause of distortion or pulsating flow, and take measures to eliminate it; 6) Display instrument failure. Troubleshooting method: repair display instrument; 7) The wiring of the display instrument is incorrect. Troubleshooting method: Correct the wiring; 8) Display instrument setting error. Troubleshooting: Correct settings; 9) The actual flow exceeds the specified flow range. Troubleshooting method: replace the flowmeter with a suitable caliber; |
Featured Turbine Flow Meters for Sale
Frequently
Asked
Questions
More Flow Measurement Solutions
Sino-Inst, Manufacuturer for Turbine Flow Meters, like: gas turbine flow meter, liquid turbine flow meter, sanitary turbine flow meter, insertion turbine flow meter, steam turbine flow meter, and natural gas turbine flow meter.
Sino-Inst’s Turbine Flow Meters, made in China, Having good Quality, With better price. Our flow measurement instruments are widely used in China, India, Pakistan, US, and other countries.
If you have any questions about Turbine Flow Meter Installation Guidelines and Troubleshooting, please feel free to contact us.
Request a Quote
Wu Peng, born in 1980, is a highly respected and accomplished male engineer with extensive experience in the field of automation. With over 20 years of industry experience, Wu has made significant contributions to both academia and engineering projects.
Throughout his career, Wu Peng has participated in numerous national and international engineering projects. Some of his most notable projects include the development of an intelligent control system for oil refineries, the design of a cutting-edge distributed control system for petrochemical plants, and the optimization of control algorithms for natural gas pipelines.