What Is a Thermal Mass Flow Meter? A thermal mass flow meter is an instrument that measures the mass flow rate of gases directly, utilizing the principle of heat dispersion. It offers accurate and reliable readings without requiring external temperature or pressure compensation. Enter the thermal mass flow meter—a pivotal tool that has reshaped the way professionals gauge flow. This instrument not only simplifies measurement tasks but also offers unparalleled accuracy, underscoring its significance in modern industrial landscapes. Join us as we delve into its workings and uncover the essence of its rising prominence.
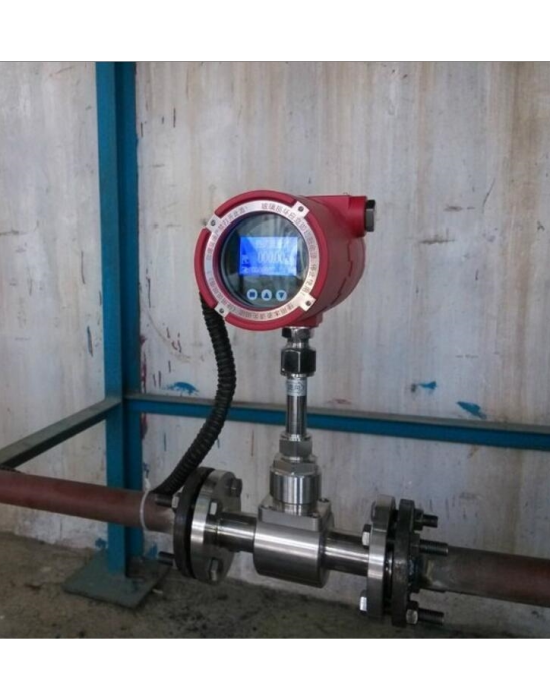
What are Thermal Flow Meters?
Thermal flow meters, known by several names like thermal meters, thermal mass flow meters, calorimetric flow meters, and thermal dispersion flow meters, all operate based on the same fundamental principle. Regardless of the terminology, they all refer to a device that uses the concept of heat dispersion for measuring flow rates.
A thermal mass flow meter is an instrument that measures the mass flow rate of gases or liquids directly, utilizing the principle of heat dispersion. It offers accurate and reliable readings without requiring external temperature or pressure compensation.
More About Thermal Mass Flow Meter Specification.
thermal mass flow meter working principle
Understanding the operation of a thermal mass flow meter boils down to grasping the idea of heat dispersion or, in more technical terms, the thermal dispersion principle.
The thermal gas mass flow meter is designed based on the principle of thermal diffusion. The instrument uses the constant temperature difference method to accurately measure gas. It has the advantages of small size, high degree of digitization, easy installation, and accurate measurement.
The sensor part of the thermal gas mass flow meter consists of two reference-level platinum resistance temperature sensors. When the meter is working, one sensor continuously measures the medium temperature T1. The other sensor self-heats to a temperature higher than the medium temperature T2, which is used for sensing The fluid flow rate is called a speed sensor.
The temperature ΔT=T2-T1, T2>T1. When fluid flows through the sensor, the temperature of T2 drops as the gas molecules collide with the sensor and take away the heat from T2. To keep △T constant, the supply current of T2 must be increased. The faster the gas flows, the more heat it takes away. There is a fixed functional relationship between the gas flow rate and the increased heat, which is the principle of constant temperature difference.
The larger the temperature difference or differential, the higher the gas flow, and vice versa. By continuously measuring this temperature difference, the thermal mass flow meter provides a real-time reading of the gas flow rate.
In essence, these meters transform the straightforward principle of heat dispersion into a reliable method for gas flow measurement, embodying both precision and technological brilliance.
Benefits of Thermal Mass Flow Meters Compared to Other Types
Direct Mass Measurement: Thermal mass flow meters excel in providing genuine mass flow readings for gases. Unlike other meters which measure volume first and then convert it to mass, these devices directly measure the mass flow. This means there’s no need for separate temperature and pressure compensation, ensuring both convenience and accuracy in gas flow measurement.
Wide Range of Measurement: These meters are versatile, capable of measuring gas flow speeds as high as 100Nm/s and as low as 0.5Nm/s. This broad range makes them particularly useful for applications like gas leak detection.
Robust and Durable: The sensors in these meters don’t have moving or pressure-sensitive parts, making them resistant to vibrations. This design ensures a long lifespan and consistent measurement accuracy, even in shaky conditions.
Easy Installation and Maintenance: One of the standout features is the ability to install and maintain these meters without halting production, provided the site conditions allow for it. This feature may require customization.
Digital Design: Embracing the digital age, these flow meters are designed with fully digital circuits. This not only ensures precise measurements but also simplifies maintenance tasks.
Advanced Communication: With RS-485 or HART communication options, these meters can seamlessly integrate into automated factories. There’s also the potential for remote wireless monitoring, with options like WeChat APP integration available.
Flexible Power Options: Users have the flexibility to choose their power source, with options including AC220V, DC24V, or a dual power source of AC220V/DC24V.
These features highlight the technological advancements and user-centric design of thermal mass flow meters, making them an optimal choice for diverse industrial applications.
What are Thermal Mass Flow Meters Used For?
Thermal mass flow meters, with their precise and consistent readings, have found their way into numerous industries and applications. Their value goes beyond just the technology; it’s about the real-world problems they solve and efficiencies they introduce.
Thermal mass flow meter applications in Industries:
- Energy & Power Generation: Monitoring and controlling fuel gas flow in power plants ensures optimal combustion and energy efficiency.
- Chemical & Petrochemical: From chemical reactions to gas distribution, the accurate measurement of gas flow is essential in these sectors.
- Pharmaceuticals: Ensuring the right flow of gases in various drug manufacturing processes guarantees product consistency and safety.
- Food & Beverage: Whether it’s the carbonation in your soft drink or the protective atmosphere in packaged foods, gas flow regulation is key.
- Environmental Monitoring: They’re indispensable in monitoring greenhouse gas emissions or managing waste treatment plants.
Based on our many years of experience in gas measurement services. We have compiled and summarized the media suitable for thermal mass flow meters for your reference:
Gases Commonly Measured with Thermal Mass Flow Meters:
- Oxygen (O2)
- Nitrogen, (N2)
- Carbon dioxide (CO2)
- Hydrogen, (H2)
- chlorine gas,
- Argon (Ar)
- Helium (He)
- natural gas,
- Liquefied gas,
- fire energy,
- compressed air
- Multi-component gas measurement
- biogas,
- Methane (CH4)
- Aeration and chlorine measurement in water treatment,
- Gases,
- Carbon dioxide gas flow rate during beer production,
- Gas flow during semiconductor chip manufacturing process,
- Gas flow measurement in solvent recovery systems
- Refrigerators
- blast furnace gas,
- coke oven gas,
- flue gas,
- During the gas process, air,
- Calcining furnace flue gas,
- Combustion gas measurement in coal-fired boilers.
- Smoke flow (speed) measurement of smoked meat (CEMS)
- Primary air, secondary air,
- Mine ventilation or exhaust system flow,
- Gas flow (velocity) measurement in heating ventilation and air conditioning systems
- And many more… (Comments are welcome to add)
If you are not sure whether you can choose a thermal mass flowmeter for your measurement conditions, please feel free to contact our Sino-Inst technical engineers!
thermal mass flow meter installation guidelines
Installation location and pipe requirements
① When installing the instrument, keep it away from elbows, obstacles, reducers, and valves to ensure a stable flow field. One side requires a longer upper straight pipe. The length of the front straight pipe is greater than 10D, and the length of the rear straight pipe is greater than 5D.
The figure below shows the length of straight pipe sections required for several situations often encountered on site.
② When the requirements for straight pipe sections cannot be met on site, gas rectifiers can be connected in series. In order to significantly reduce the requirements for straight pipe sections.
Installation of insertion flow meter with ball valve
① Open a 20~22mm hole in the pipe, and then weld the base to the hole with the base flow meter.
② After opening the ball valve, screw one end of the ball valve to the external thread welded to the base of the pipe (check the lock to prevent leakage), insert the probe rod and tighten the locking head (pay attention to the flow direction).
③When inserting the probe rod, pay attention to the insertion depth: insertion depth = A-B (1/4~1/2 of the inner diameter of the pipe).
④ If the medium contains moisture, oil or impurities, please refer to the figure below for installation (45 degrees below the pipe).
Installation of pipeline flow meter
Customers of pipeline flow meters do not need to select the insertion depth. They only need to select the flow rate corresponding to the diameter in the flow range table. When installing, just connect the flange (thread or clamp) of the flow meter to the pipe and fix it.
Selection Guide
Based on our many years of experience at Sino-Inst. We recommend that you consider the following measurement parameters when selecting a thermal mass flowmeter:
- Installation form: such as pipeline installation, plug-in installation, threaded installation, flange installation, etc.
- Pipe diameter (square pipe or round pipe)
- Conditions of the medium being measured
- Sensor material requirements
- Pressure and temperature inside the pipe
- What signal output is needed?
- Power supply requirements: Generally 24VDC, or 22VAC
- Explosion-proof requirements, etc.
FAQ
More Flow measurement technologies
Flow Meter Straight Length Requirements Guide
What Is Density Flow Meter: Principles and Applications
What Is a Turbine Flow Meter for Gas? and Why Choose It?
The Role of Gear Flow Meters For Cement Additives
Buyer’s Guide to Industrial Fertilizer Flow Meters
What is an Ammonia Flow Meter and How to Choose?
Thermal mass flow meters, with their precision, durability, and wide applicability, have emerged as a front-runner in gas flow measurement. But the scope of modern measurement tools doesn’t end here. Advancements in technology have also paved the way for specialized instruments in other areas. For those involved in the oil industry, understanding crude oil flow measurement is crucial. Likewise, ensuring accuracy in liquid level measurement and temperature measurement can make all the difference in various applications, ensuring safety, efficiency, and product quality.
At Sino-Inst, our journey extends beyond just offering products. With a rich tapestry of experience, we stand as a leading manufacturer and supplier in the instrumentation arena. Whether you’re seeking standard instruments or looking for customized solutions tailored to your unique requirements, our team is here to assist.
Request a Quote
Wu Peng, born in 1980, is a highly respected and accomplished male engineer with extensive experience in the field of automation. With over 20 years of industry experience, Wu has made significant contributions to both academia and engineering projects.
Throughout his career, Wu Peng has participated in numerous national and international engineering projects. Some of his most notable projects include the development of an intelligent control system for oil refineries, the design of a cutting-edge distributed control system for petrochemical plants, and the optimization of control algorithms for natural gas pipelines.