What Is Turbine Flow Meter?
A turbine flow meter capitalizes on the fluid’s mechanical energy, employing a precisely designed rotor that rotates within the flow path. This rotor’s rotational speed, intricately linked to the fluid’s velocity, offers an accurate measurement scale. Deployed across diverse industries, turbine flow meters stand as trusted instruments, delivering reliable measurements for not just liquids but also gases, underscoring their versatility and precision.
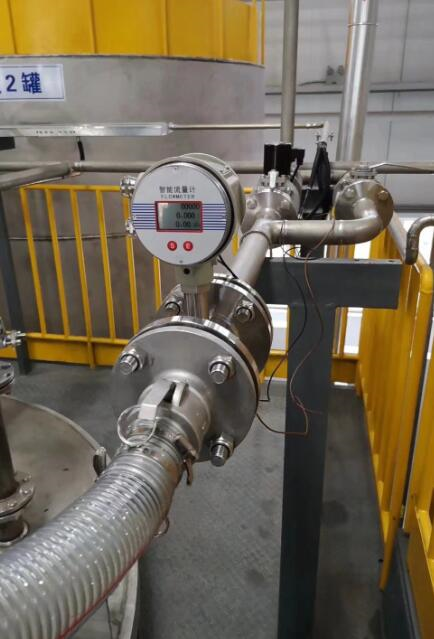
Featured Turbine Flow Meters
How Does a Turbine Flow Meter Work?
When the fluid flows through the sensor housing, since the blades of the impeller(rotor) are at a certain angle to the flow direction, the impulse of the fluid causes the blades to have a rotational torque. After overcoming the friction torque and fluid resistance, the blades rotate. After the torque is balanced, the rotational speed becomes stable.
Under certain conditions, the rotational speed is proportional to the flow rate.
Since the blade is magnetically permeable, it is in the magnetic field of the signal detector (composed of permanent magnet steel and a coil). The rotating blade cuts the magnetic lines of force, periodically changing the magnetic flux of the coil. This causes an electrical pulse signal to be induced at both ends of the coil. This signal is shaped by the amplifier to form a continuous rectangular pulse wave with a certain amplitude. It can be remotely transmitted to the display instrument to display the instantaneous flow rate or cumulative total volume of the fluid.
Within a certain flow range, the pulse frequency f is proportional to the instantaneous flow rate Q of the fluid flowing through the sensor. The flow equation is:
Q=3600*f/k
In the formula:
f—Pulse frequency [Hz]
K-sensor instrument coefficient [1/m3], given by the calibration sheet.
Q-instantaneous flow rate of fluid (under working condition) [m3/h]
3600-conversion factor
The instrument coefficient of each sensor is filled in the calibration certificate by the manufacturer. The K value is set into the matching instrument. The instantaneous flow and cumulative total can be displayed.
How Accurate are Turbine Flow Meters?
When it comes to flow measurement, accuracy is paramount. Among the various tools and instruments available, turbine flow meters are often the choice for many industry professionals. But how do they stack up in terms of accuracy? Let’s dive deep and shed light on this critical aspect.
The Basics of Turbine Flow Meter Accuracy
At its core, a turbine flow meter’s accuracy is determined by its ability to measure flow velocity reliably. Generally, these meters boast an accuracy range of ±0.5% to ±1% of reading for liquids and ±1% to ±2% for gases under optimal conditions.
Factors Influencing Accuracy
Several elements come into play that can influence the precision of turbine flow meters:
- Fluid Properties: Variations in viscosity, especially in liquids, can impact rotor spin and subsequently, measurement accuracy.
- Flow Profile: Turbulent or laminar flow profiles can influence the meter’s readings. Proper installation, away from bends and valves, can help maintain a stable flow profile.
- Calibration: Calibration specific to the fluid being measured ensures that any discrepancies related to fluid properties are accounted for.
Turbine Flow Meter Types and Their Accuracy
Different designs and models cater to specific applications, each offering varying degrees of accuracy:
- Liquid Turbine Flow Meters: Often achieve accuracy up to ±0.5% of reading.
- Gas Turbine Flow Meters: Generally offer accuracy in the range of ±1% to ±2%.
What Does a Turbine Type Flow Meter Generate?
As we discussed earlier, the Turbine Flow Meter will generate pulses. The essence of a turbine-type flow meter lies in its ability to generate electrical pulses that correspond with fluid or gas flow rates. But what exactly is this output?
- Pulse Generation – The Heartbeat of the Meter
The fundamental output of a turbine flow meter is a series of electrical pulses. As fluid or gas courses through the meter, it drives the turbine rotor, causing it to spin. Each rotation, or even a fraction of it, generates a distinct pulse. - How Pulses Relate to Flow
The rate at which these pulses are generated directly correlates with the flow rate of the fluid or gas. A higher flow rate will lead to a quicker rotor spin and, consequently, a higher pulse frequency. Conversely, a slower flow results in a reduced pulse frequency. - Sensing Mechanisms – Translating Motion into Electrical Output
Positioned adjacent to the rotor is a sensor, typically magnetic or optical. As the rotor blades spin, they disrupt the sensor’s field, creating an electrical pulse. The frequency of these pulses, hence, represents the fluid velocity and is the primary data output. - Converting Pulses to Meaningful Data
While the raw pulse frequency offers insights into flow rate, advanced electronic systems within the meter transform these pulses into actionable data. This can be displayed as volume per unit of time, totalized volume, or other relevant metrics, depending on the application. - Additional Outputs
Modern turbine flow meters often come equipped with capabilities beyond basic pulse generation. Some may offer analog outputs, like 4-20mA signals, which can be integrated into control systems. Others might feature digital outputs for more sophisticated monitoring or control setups.
What are the Advantages of Turbine Flow Meters?
Turbine flow meters, renowned for their precision and adaptability, bring a suite of benefits to industrial processes:
- Cost-Effective: Generally, they are more economically priced when benchmarked against other advanced flow measurement technologies.
- Swift Responsiveness: These meters exhibit an impressive response time, with repeatability rates as high as 0.05%, ensuring reliable measurements.
- User-Friendly Installation and Upkeep: Their design facilitates straightforward installation and minimal maintenance, reducing downtime.
- Adaptable Mounting: Universal mounting positions offer flexibility during setup, accommodating varied industrial requirements.
- Direct Measurement: They provide direct volumetric flow measurements, eliminating the need for complex conversions.
- Advanced Monitoring: Many models are compatible with cutting-edge monitoring electronics, enabling data analytics and real-time tracking.
- Efficient Flow Dynamics: Their design results in minimal pressure drops, ensuring energy-efficient operations.
- Low Flow Sensitivity: These meters can detect flow rates as low as 0.01 feet per second, ensuring accurate measurements even at reduced flow rates.
- Wide range of use: Liquid turbine flowmeter can be made into an insertion type, suitable for large diameter measurements. Small diameter can be up to DN4.
- Strong compatibility: For different media, there are 304 stainless steel, 316 stainless steel, PE materials, etc. available.
- Customizable: Extremely low temperature (-196℃) and high temperature 180℃ can be customized. High pressure 16MPa, 25Mpa, 32Mpa, etc. can be customized.
What are the Disadvantages of Turbine Flow Meters?
While turbine flow meters offer numerous benefits, certain considerations can influence their suitability:
- Wear due to Over-Ranging: Operating beyond the meter’s maximum flow rate can accelerate wear, affecting its lifespan.
- Sensitivity to Contaminants: Certain models necessitate upstream filtering of ferrous particles to maintain accuracy. Moreover, magnetic particulates in fluids can hinder the output signals in some variants.
- Full Pipe Requirement: For optimal accuracy, pipes must remain consistently full, as partial flows can skew readings.
- Directional Limitations: By default, many models measure unidirectional flows. However, select advanced models can accommodate bi-directional flows.
- Optimal Media Conditions: They are ideally employed for clean media with low viscosities. High particulate or viscous fluids can challenge accuracy.
- Piping Considerations: To diminish flow turbulence, which can impact accuracy, they demand certain straight piping prerequisites upstream and downstream.
What are some applications for turbine flow meters?
Turbine flow meters, with their ability to provide rapid and accurate flow measurements, have found utility across a multitude of industries and applications. Below are some application introductions compiled based on our many years of service experience at Sino-Inst. Comments are welcome to add.
Oil and Gas Industry:
Oil Refineries: Turbine flow meters are pivotal in oil refineries for the precision measurement of crude oil and refined petroleum products.
Gas Distribution: They facilitate the measurement of gas flow rates, essential for billing and distribution.
Water Treatment Plants:
Monitoring and controlling water flow is crucial in these facilities, ensuring that adequate treatment processes are adhered to. Turbine flow meters serve this purpose by offering precise flow rate data.
Aerospace:
In the domain of aviation fuel testing, turbine flow meters ensure that the correct volume of fuel is dispensed, keeping safety and efficiency at the forefront.
Pharmaceuticals:
In drug manufacturing processes where specific volumes of liquids need to be transferred or mixed, these meters provide invaluable data, ensuring that the formulations are consistent and effective.
Dairy and Food Processing:
Turbine flow meters play a significant role in measuring the flow of milk, juices, and other liquid food products, ensuring quality control and correct product quantities.
Chemical Plants:
When it comes to transporting aggressive or corrosive liquids, turbine flow meters offer reliable readings, ensuring that processes remain within desired parameters.
Agriculture:
For irrigation systems, accurately measuring water flow is crucial. These meters ensure that fields receive the optimal amount of water, promoting effective crop growth.
Hydraulic Testing:
Engineers rely on turbine flow meters for hydraulic system testing to ensure that systems operate under designated flow conditions.
Extremely low temperature conditions:
Low-temperature turbine flowmeters are also used for flow measurement of liquid nitrogen, liquid hydrogen, and liquid oxygen.
Are Turbine Flow Meters Suitable for Water?
Turbine flow meters shine in measuring clean, low-viscosity liquids, making them well-suited for water flow assessments. Their precision in water measurements is commendable, often surpassing other mechanical flow meters. However, for optimal performance, it’s crucial to ensure the water is free from large particulates that might obstruct the turbine, as well as devoid of magnetic particles and iron which could skew readings. When these conditions are met, the turbine flow meter remains a reliable choice for accurate water flow evaluations.
What Other Liquids Can Turbine Flow Meters Measure?
Beyond water, turbine flow meters have carved a niche in measuring a diverse range of liquids, proving their versatility in various industrial contexts. Their precision and adaptability make them a go-to choice for several liquid applications. Here are some prominent liquids that these meters effectively gauge:
- Hydrocarbons: Fuels like diesel, petrol, and aviation fuel are commonly measured using turbine flow meters. Their consistent viscosity levels at operational temperatures make them an ideal fit.
- Chemicals: From solvents like acetone and benzene to more viscous chemicals like glycol, turbine meters can handle a wide spectrum of chemical fluids, provided they’re free from impurities that could hinder measurement.
- Alcohols: Ethanol, methanol, and other alcohols, often used in industrial processes or as fuels, can be accurately gauged with these meters.
- Pharmaceutical Liquids: Turbine flow meters cater to the pharmaceutical sector by measuring liquids like saline solutions, syrups, or even certain liquid medications.
- Food & Beverages: The food industry employs turbine flow meters for liquids like vegetable oils, fruit juices, and even dairy products, given the sanitary configurations available.
- Lubricating Oils: The lubricant industry benefits from turbine flow meters, using them for measuring various grades of lubricating oils.
- Cryogenic Liquids: With special configurations, these meters can even handle supercooled liquids, such as liquid nitrogen or liquid oxygen.
In conclusion, turbine flow meters are not just limited to water. Their broad spectrum of applicability across multiple industries, from petrochemicals to food processing, underlines their versatility and efficacy. However, always ensure compatibility and consider the specific requirements of each liquid for optimal measurement accuracy.
Can turbine flowmeter measure gas?
Turbine flow meters, while primarily designed for liquid measurements, are also adept at gauging the flow of gases. When tailored with appropriate design modifications and calibrated correctly, these meters can accurately measure various gases, from industrial to natural.
Takes into account the compressibility of the gas, the change in volume, temperature and pressure of the medium directly converts the flow under the working condition into the flow under the standard condition to ensure the accuracy of the measurement.
Our Sino-Inst gas turbine flowmeter is suitable for gas measurement in the fields of petroleum, chemical industry, aerospace, scientific research department, chemical industry and so on. It can be used for the measurement and measurement of natural gas, coal gas , propane, air, nitrogen and other gases. Used for trade measurement between users and process control between industrial production.
Are Turbine Flow Meters Inline or Insertion?
Turbine flow meters, given their versatility and adaptability, can be found in both inline and insertion models。Here’s a refined explanation of their distinct attributes:
Inline Turbine Flow Meters:
Popularity: These are the prevalent choice, especially when considering smaller pipeline sizes.
Design & Efficiency: Designed for a direct flow path, they offer an unobstructed measurement environment, ensuring maximum accuracy and efficiency.
Applications: Best suited for pipelines with smaller diameters, where precision is paramount.
Insertion Turbine Flow Meters:
Cost-Effectiveness: For those managing larger pipelines or higher flow velocities, insertion models are a more economical choice due to their design that doesn’t necessitate a complete flow body.
Installation: The process involves making a hole in the pipeline to insert the measuring probe. The electronics are then secured to the pipe via an integrated fitting.
What are the Straight Pipe Requirements for Turbine Flow Meters?
In order to eliminate the influence of liquid vortex and uneven cross-sectional flow velocity on the measurement, necessary straight sections or rectifiers should be installed at the inlet and outlet of the sensor.
Generally, the length of the straight pipe section in the upstream part (inlet) is required to be (15~20)D (D is the nominal diameter of the sensor).
The length of the downstream part (the straight pipe section at the outlet) is 5D, and the diameter of the straight pipe and the diameter of the sensor must be the same, otherwise it will cause measurement errors.
In addition, the length of the straight pipe section in the upstream part should be determined based on the status of the piping in front of the sensor. The general recommendations are as follows:
Do Turbine Flow Meters Have Digital Displays?
The turbine flowmeter can be configured with a local digital display. The LCD display can display instantaneous flow, accumulated flow, flow rate, etc.
Some customers only need signal output and do not need local display, so they will not configure a monitor.
Do Turbine Flow Meters Have Switches?
If you are purchasing a battery powered turbine flow meter. Then there is a switch for battery power.
If you are referring to the turbine flowmeter as a flow switch. So. Turbine flow meters sometimes offer integral or optional flow switch capabilities.
What is the K-Factor of turbine flow meter?
Definition of K-Factor:
The K-Factor of a turbine flow meter defines the number of pulses the meter will produce for a specific volume or mass of liquid passing through it. It’s typically expressed in pulses per gallon (PPG) or pulses per liter (PPL), depending on the unit of measure.
Significance in Flow Measurement:
By utilizing the K-Factor, one can accurately convert the number of pulses generated by the turbine flow meter into a quantifiable flow rate. This value is crucial when configuring flow meter transmitters or integrating the flow meter into process control systems.
Deriving the K-Factor:
To determine a turbine flow meter’s K-Factor, the meter is calibrated under controlled conditions using a fluid with a known density and viscosity. The number of pulses produced is then divided by the volume of fluid passed to derive the K-Factor.
Generally, after we produce the turbine flowmeter, we will calibrate it and standardize the corresponding K coefficient on the flowmeter.
Factors Influencing K-Factor:
- Fluid Properties: Changes in fluid density and viscosity can influence the K-Factor.
- Meter Wear: Over time, wear and tear on the turbine blades can alter the K-Factor.
- Flow Profile: Turbulence or varying flow profiles can affect the accuracy of the established K-Factor.
How Much Do Turbine Flow Meters Cost?
How Much Do Turbine Flow Meters Cost?
Ok. This is probably what most readers want to know.
First of all, the price of turbine flow meters is not constant. Depending on the measurement parameters, there will be different configurations. Then the price of turbine flow meter will also be different.
Here, we provide you with a reference price:
Liquid turbine flow meter
DN15
DC24V
Output two-wire system 4~20mA
LCD displays instantaneous flow and cumulative total
Body materialPE
Flange connection
Flow range 0.6~6m3/h
Accuracy 0.5%
Temperature resistance 65℃
Pressure resistance 1.0Mpa
ExdIICT6Gb explosion-proof
FOB Price USD 390.00/set
More Flow Measurement Solution
What Is a Turbine Flow Meter for Gas? and Why Choose It?
Turbine Flow Meter Application Case: Demineralized Water
Turbine Flow Meter Installation Guidelines and Troubleshooting
Liquid Turbine Flow Meters
Buyer’s Guide: Flow Technology-Turbine Flow Meter
Turbine Flow meter Vs Gear Flow meter
At Sino-Inst, we’re not just limited to turbine flow meters. We pride ourselves on our expansive range of instruments tailored for crude oil flow measurement, liquid level measurement, and temperature monitoring. With a rich heritage backed by experience, we’ve established ourselves as leading manufacturers and suppliers in the industry.
When it comes to reliability and accuracy, our instruments stand out. Our dedication to excellence stems from our profound expertise, ensuring that our clients receive products that not only meet but exceed their expectations. Looking for something unique? We offer customization to cater to your specific needs.
Contact us today and let our experts guide you to the perfect solution for your measurement challenges. Experience the Sino-Inst difference!
Sources:
Flow Measurement
Industrial Flow Measurement Basics and Practice
Request a Quote
Wu Peng, born in 1980, is a highly respected and accomplished male engineer with extensive experience in the field of automation. With over 20 years of industry experience, Wu has made significant contributions to both academia and engineering projects.
Throughout his career, Wu Peng has participated in numerous national and international engineering projects. Some of his most notable projects include the development of an intelligent control system for oil refineries, the design of a cutting-edge distributed control system for petrochemical plants, and the optimization of control algorithms for natural gas pipelines.